How to avoid the most common costly errors when spec’ing work trucks
Properly spec’ing a work (vocational) truck for its particular mission or application is essential. That is how to get the most durability and productivity, plus easy maintainability, out of the vehicle at the lowest cost of ownership. Otherwise, when not designed to meet specific requirements, the outcome will be higher operating costs as a result of inefficiency, mechanical failures and vehicle and driver downtime.
There are several fundamental steps to truck selection and spec’ing that will avoid the most common mistakes in designing a work truck, say OEM truck, body and equipment manufacturers and suppliers.
Step #1 – Review
Review how the current work trucks are performing, officials advise. Examine the performance of the current units, keeping an eye out for any particular issues or problems that may need to be addressed in the new trucks. Scrutinize truck maintenance records for repeated problems, breakdowns, unscheduled downtime, etc.
Furthermore, say officials, visit with vehicle technicians and truck drivers. They can provide insight into any deficiencies with current vehicles and may be able to offer suggestions for changes to improve safe operation and productivity.
All this gathered intelligence can be used to eliminate past issues and address any uncovered weaknesses to help to reduce maintenance costs and increase productivity by cutting unnecessary downtime.
Step #2 – Correct Specs
Experience shows that common causes of unplanned work truck downtime and repair are problems due to the powertrain not being right for the application, an under-spec’d vehicle and overloading. These situations will decrease efficiency, increase maintenance costs and downtime, plus heighten liability risk if the truck is involved in a preventable accident.
Usually, observe the officials, vocational trucks are under-spec’d to save on acquisitions costs and/or to avoid exceeding a gross vehicle weight rating (GVWR) of 26,000 lbs. Vehicles with a higher GVWR require drivers to have a Commercial Driver’s License (CDL) and with that comes the need for compliance with increased regulatory requirements.
On the other hand, over-spec’ing – usually done because fleets think it will result in greater truck longevity – increases operating and capital costs.
Step #3 – Functional Requirements
Another fundamental in the work truck spec’ing process is determining if the functional requirements for the truck’s job – what the vehicle is expected to do and how – have changed. Among the questions to address:
- Have the operating parameters changed?
- Are there new regulations (federal, state and local) that impact truck design and operation and will necessitate revision of the work truck specifications?
- Are new products and technologies available that can help improve truck productivity and lower operational costs?
Step #4 - Advice and Guidance
A best practice is to always consult with OEM truck, body and equipment manufacturers and suppliers for their advice and recommendations when making work truck equipment decisions. It is their job to keep up with vehicle and equipment changes.
Communicating with them about a truck’s application requirements and operating parameters, and desired performance expectations, will enable them to suggest the most appropriate chassis, body and components to maximize efficiency, reliability, durability and safety of the completed work truck.
What’s more, by working together early in the process, body installation and upfit time can be reduced, and that helps lower acquisition costs.
Don’t forget to factor in production lead times for vehicle chassis and body building to ensure that the new work truck is ready when needed, officials emphasize. The more custom the work truck, the longer the order-to-delivery time.
Step #5 – No Duplication
Some fleets fall into the easy trap of replacing an existing vehicle by just duplicating the old unit, observes Robert “Bob” Johnson, director of fleet relations for the NTEA, the Association for the Work Truck Industry (www.ntea.com). That truck may not have been optimized for the job it is doing.
But “even if the vehicle was properly spec’d at the time it was initially acquired, requirements change and new and improved products are constantly being introduced,” he points out. “It is possible that there is a new body, chassis or piece of equipment that would offer significant improvements over what was previously available.”
Johnson stresses that chassis selection, in particular, should be carefully thought through every time because chassis specifications change from year to year. By way of example, a current Class 6 chassis may not have the same net payload as an older Class 6 chassis from the same OEM.
Step #6 – Body before Chassis
Too often, fleets “begin the specification-writing process with the truck chassis, when it is most logical to address the body and equipment first because an effective, productive work truck is designed to perform a specific job or series of jobs,” NTEA’s Johnson says. Hence, it “makes sense to start the process by defining the job or jobs the truck will perform. From there, you can address the equipment and associated truck body needed to perform those tasks.
“Finalizing the body and equipment will define the vehicle’s required payload, necessary clear cab-to-axle chassis length and the loaded body’s center of gravity. “This information enables you to select an appropriately sized chassis.”
Additional considerations are overall truck and body dimensions, maneuverability and turning diameter requirements.
Step #7 – Weight
Consideration of the chassis needs to include whether the GVWR will satisfy the payload requirements and if the gross combined weight rating (GCWR) is adequate if the truck will be towing a trailer.
There is also the matter of gross axle weight rating (GAWR) – the value specified by the vehicle manufacturer as the load-carrying capacity of a single axle system. Each axle on a truck and trailer has a maximum allowable weight capacity.
After the preliminary selection of a suitable chassis has been made, perform a detailed weight distribution and payload analysis to determine individual axle loadings, advises Johnson of NTEA. When necessary, optional axles, suspension components and frames may be required to ensure that the chassis is not overloaded and all equipment-mounting requirements have been met.
Step #8 – Powertrain
“Once the correct foundation components have been selected, it is time to move on to the powertrain – engine, transmission, axle ratio, etc. – and other components, such as the electrical system, fuel tanks and cab content,” Johnson says. “All of these components have an impact on the completed vehicle’s overall performance and productivity, so it is important to make selections based on valid requirements.”
He notes that in far too many cases, fleets make powertrain selections based on guesses instead of a careful analysis of horsepower and engine torque demands. He recommends starting by defining the desired performance criteria:
- Road (cruising) speed.
- Starting gradability – the steepest grade that a vehicle can start on (launch) in its worst-case design condition.
- Reserve gradability – the maximum grade a vehicle can climb in its highest gear without losing road speed, etc.
Then, the actual requirements should be calculated.
“This will allow you to select the proper engine, transmission and axle ratio to ensure that the truck performs as required,” says Johnson. “The payoff in this process is a truck that has better fuel economy and lower maintenance costs.
“The powertrain design process is not difficult, but is critical that you know how much the completed vehicle will weigh, including trailers for combination vehicles, and that you make realistic selections when establishing your performance criteria. Chassis dealers have access to sophisticated computer programs that will make these calculations for you, but the output is only as good as the information you put in.”
Step #9 – Maintainability
Not to be overlooked during the spec’ing process, says NTEA’s Johnson, is incorporating maintainability into work truck specs as this “can result in significant reductions in life cycle maintenance costs, primarily as a result of decreased labor expenses.”
Maintainability and reliability are two separate issues, he explains. Products can be made more reliable by specifying more durable components and materials and by adding devices, such as overload protection to a unit. “Unfortunately, these steps usually add cost and/or weight to your trucks.
“Maintainability, on the other hand, addresses the ease with which a unit can be maintained and repaired when needed. It also encompasses the planning you can incorporate into the design to reduce maintenance issues not associated with operational component or material failure.”
He says that in general, there are three major components of maintainability:
- Preventative design – Consider how drivers/operators use the truck and equipment and take steps to ensure that real-world use will not result in failures that aren’t associated with the intended use of the equipment.
- Ease of service – This results in:
+ Fewer labor hours incurred for each scheduled service.
+ Increased likelihood that the equipment will receive the required service because it is easier to service in the first place.
+ Reduced chance of a breakdown, since the equipment is being serviced on a timely and regular basis.
- Ease of component replacement – Try to identify the components that may have to be replaced during the life of the unit and be sure to specify that these items, where applicable, are mounted using screws, nuts and bolts or removable rivets because the longer trucks are kept, the more likely there will be mounting issues.
Step #10 – Hydraulic Hoses
Because hydraulic hoses will eventually need to be replaced, NTEA’s Johnson says that “a little forethought can make this task much easier. Insist that the upfitter lay hoses parallel, as opposed to twisted around each other. Not only does this reduce hose damage, but when you do have a failure, you can often attach the new hose to the old one and use it to pull the new hose into place.
“If a large number of hoses come together at a manifold or valve bank, tell the upfitter to alternate between long and short body couplings so that you will have adequate wrench room to loosen/tighten the fittings.”
BE PREPARED
It is common knowledge that doing homework pays off big. Before starting the work truck spec’ing process, it is paramount to invest the time and effort necessary to gain:
- A clear understanding of the truck work’s needs.
- Application and mission requirements.
- Operating environment.
- Desired performance.
- Maintenance requirements.
- What specs worked and didn’t work in the past.
While initial cost is a major consideration when making truck and equipment acquisition decisions, total cost of ownership (TCO) should be contemplated as well. That means factoring in all direct and indirect costs expected to be incurred during the life of the truck, including such things as financing, insurance, utilization, maintenance and repair, projected resale value, etc.
Acquiring a new work truck is a big investment. Making the effort to ensure that the vehicle is optimized for its specific purpose will result in a more productive, cost-effective vehicle, and that, in turn, can make a big difference on life cycle costs.
About the Author
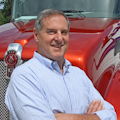