I was part of a select group of North American truck journalists invited by Meritor to visit its axle manufacturing plant in Cameri, Italy, late last month.
That is one of four manufacturing plants that the company – a leading global supplier of drivetrain, mobility, braking and aftermarket solutions for commercial vehicle and industrial markets – has throughout Europe. The others: an axle plant in Lindesberg, Sweden; a truck brake plant in Cwmbran, United Kingdom (which I had the opportunity to visit last year); and a plant in Vénissieux, France, that produces axle castings and forgings.
The Cameri plant has an interesting history. It began as a flight school, then became an aircraft production facility. It then got into bus production before evolving into the manufacture of axles. The plant’s first axle came off the assembly line in 1983.
Modernization
Nowadays, the Cameri plant’s than 530 workers produce fabricated and casted carriers, axles, gear sets, drum brakes and differentials.
The voluminous, clean plant is impressive. Robots for various steps in the manufacturing process are prevalent. Millions have been invested by Meritor over the past several years to upgrade and modernize the plant.
Meritor’s axle line cover light through extra heavy duty vehicles.
Tech center
Housed in a separate building at the Cameri facility (the hanger that once was used to store produced aircraft) is the testing and prototype lab. Among other things, the lab assembles prototypes, performs noise analysis and does product validation and testing.
Equipment includes two axle dynamometers (600 horsepower and 700 horsepower); a hub-reduction dynamometer, a machine for housing spindle fatigue side skid testing; setups for checking axle lubrication, oil flow optimization and axle housing integrity; devices for testing hub rotary fatigue and axle shaft torsional fatigue; a brake inertial dynamometer; a brake chucker; and a vibration rig.
The final element in Meritor’s testing program is vehicle testing, wherein Meritor engineers subject their products to intensive vehicle testing at both test circuit and road test conditions, Marco Bassi, Meritor’s senior director, Europe and South America engineering, told me at the end of the plant tour.
Both have individual benefits, he explained. The test track provides a fully controlled environment. Road testing however, especially Alpine mountain circuits, provides a “rigorous, punishing environment totally reflective of actual usage.”
I always enjoy plant tours because it provides me with a better appreciation of all the engineering, testing and validation that goes into product development.
About the Author
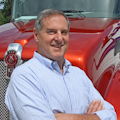