How could I know a 2005 conversation with my kids’ elementary school principal would be one of the most important conversations of my life, and lead to becoming a full-time advocate for idle-reduction behavior modification among commercial vehicle fleets?
I couldn’t, because at the time I had no idea about the deleterious downstream costs of idling behavior in fleet management, from how the atmosphere is impacted to the excessive wear and tear on engines.
On that winter day, the principal recounted how the faculty and students would get nauseous each day at around the same time. They couldn’t figure out why. Turns out the cause was idling school buses. It immediately struck me how parents also idled continuously outside the school, with the exhaust from all those cars and buses vented inside the classrooms.
I also witnessed that when most moms and dads were recruited by their kids to ‘go idle free’ (through a campaign we started), they dropped their old habits like a hot lug nut. Fast forward to today and my role has become educating fleets about the downstream costs of continuous idling behavior on our fleet and personal vehicles, which has caused fleets to change their ways as well.
If the argument about making the air cleaner for our kids was successful, then the data about costs to the fleet and burden on the maintenance department will impact fleets. The North American Council on Freight Efficiency found a Class 8 tractor idling five to eight hours a day for 300 days per year creates 24,000 lbs. of CO2 while using 1,200 gallons of diesel. And the American Trucking Associations concluded an idling engine has double the wear and tear of one in motion, which increases maintenance cost by at least $2,000 per year. Cummins reported that engine life can be reduced by up to 20%. These costs are particularly pernicious in fleet diesel assets with expensive aftertreatment systems. A fleet of 500 trucks spends $27,000 every month on emissions repairs, according to the ATA.
Other downsides include compromised warranties (due to preventive maintenance schedules planned on miles versus hours), lifecycle costs, vehicle downtime, employee productivity, and fleet reputation due to excessive emissions output.
The problem is large and so is the payoff to fixing it. First, fleet managers should step back and subdivide the challenge of idle reduction into two segments: new vehicles and legacy vehicles. In new equipment, fleet managers have a growing number of choices directly from OEMs. The downside is that managers have limited capital to purchase the likes of electric vehicles (EVs).
Internal research from my consulting firm, GoGreen Communications, tells us that about 9.5% of the fleet in North America is replaced annually. This means that it could be three years before even a third of a manager’s fleet is replaced with more fuel-efficient vehicles like EVs. So, replacement programs through acquisitions are a long-term solution.
On the legacy equipment side, there’s mechanical and programming solutions known today as Idle Reduction Technologies (IRT). Examples include idle timer/limiters, auto engine shut-down/start-up systems, auxiliary power units (APUs), fuel- or battery-powered AC/heat, telematics (for tracking driver behavior and cost metrics), programmable rpm solutions, and alternative fuels such as propane and CNG.
However, the 800-lb. gorilla in the room regarding legacy fleet fuel efficiencies is modifying your driver’s mindset and how they approach their portion of the fuel efficiency puzzle. And that is driver idle-reduction behavior modification. From our research here at GoGreen Communications Inc., the typical fleet operator in North America is spending about 40% of their fleet’s engine hours on driver idling behavior of some kind. The biggest piece of that idling pie is driver idling ‘by choice’, which we estimate can be eliminated by at least 80% in every fleet operation. In our view, idling is the biggest and most immediate cost avoidance metric in fleet operations today.
As tempting as it is to look to the future and a point in time when our fleets will be all electric, the fact is that dramatic improvements in fuel efficiency and emissions reduction in a manager’s legacy fleet are available right now. A well-managed idle reduction behavior modification program will produce phenomenal savings in a relatively short period of time.
These initiatives can quickly pay for themselves within the first year, while the reductions in greenhouse gas emissions and exhaust pollutants from ‘driver choice idling' are typically enormous. And the icing on the cake? Fleet operators will feel really good about their drivers reducing costs and emissions at work, and their idling behavior around their kids' schools too.
About the Author
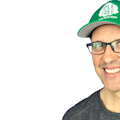
Ron Zima
Ron Zima, the CEO of GoGreen Communications, is a former cross-Canada radio / TV host and creator of IDLE FREE for our kids, a cause which began at his kid's elementary school in 2006. Since then, Ron and the GoGreen Communications team have transformed fleets and businesses to become IDLE FREE champions, helping them reduce fuel use and emissions while improving air quality in their communities.
Ron has created the fleet management category of ‘idle reduction behavior modification’ for fleet operators and is now recognized as the expert on idle management, branding, and public relations for corporate fleet operators.