How to increase uptime with filter monitoring
Inflation and continued supply chain strains are driving up costs, particularly on replaceable engine parts. Proper engine maintenance will ensure parts last longer and the system runs at peak performance. This is the job air and fuel filters were made for, so a smart strategy is to make sure these also operate at an optimal level.
One option is to have technicians perform more frequent engine checks, but with the shortage of qualified repair technicians, this could leave other tasks undone. The less labor-intensive solution is to deploy a continuous filtration monitoring solution. Recent advances in sensor technology, along with the wider use of telematics and data analytics, are making this possible and helping prevent downtime caused by poor filtration.
These solutions continuously look for a dip in performance and alert fleets. This allows fleets to proactively schedule a filter change that, if left unchecked, could put undue stress on the engine. Even if this doesn’t lead to a costly roadside event or unscheduled maintenance, the truck will lose fuel efficiency and increase the fleet’s fuel expense.
Continuously monitoring your filtration helps to not only minimize costly, unwanted downtime, but also unchains your operations from a time-based schedule to a condition-based one, often reducing the number of filters you need to purchase and stock each year. The savings can really add up across an entire fleet.
With this said, let’s focus on the two different types of filtration monitoring for your over-the-road vehicles: air and fuel.
Particulate air filters
Diesel soot, dust, dirt, and pollen are all filtered out of a vehicle’s cabin through its particulate filters. With these filters capturing the largest pollutants, and because of the importance of air filters to the health and safety of both the operator and the truck, they will need to be cleaned or replaced in a routine manner.
Unfortunately, many truck operators don’t check their dirty air filters and end up having downtime problems as consequence. Whether you are an operator or a fleet manager, become educated on this matter and properly maintain your vehicles for health, safety, and equipment performance.
An important area to start this education is the diesel particulate filter (DPF), which captures and stores particulates in its cylindrical-honeycomb structure. Those captured particulates must be occasionally burned off to regenerate the filter. If your DPF were to fail due to poor servicing or maintenance, particulates could get to your vehicle’s core system and cause damage over time, resulting in unplanned downtime or even engine failure.
Replacing an air filter can be expensive—but replacing an engine system is even more expensive. You are protecting hundreds of thousands of dollars of equipment by investing in suitable filters and filtration monitoring.
Fuel filtration
If you aren’t replacing the diesel filter consistently, it can force the engine to use more fuel to get power and acceleration, which can wear the engine down. Nowadays, creating filter replacement intervals based on data instead of a blanket number of miles can be vital to cost reduction and proper fleet maintenance.
Something highly desirable to equipment owners in today’s market is saving money on service. Most of the maintenance that needs to be done can be serviced straight from your truckyard to avoid high maintenance costs. Check in with an external partner that can help you monitor your engine’s diesel fuel through digital maintenance monitoring systems for maximum operating performance and efficiency.
The solution: predictive monitoring
The greatest way to monitor your diesel engines is through predictive maintenance monitoring tools that give you a complete overview of your equipment with engine analytics and location services. For a better understanding of what you may be able to benefit from by using these external services, you may want to research the digital maintenance services used by many top companies.
In trucking and transportation, equipment reliability is essential for profit maximization and deadline completion. With this proactive approach, you’ll worry less about diesel soot and improve uptime with predictive maintenance tools to increase how many miles your equipment travels per quarter. These condition-based monitoring tools allow you to spend more time on what matters most—moving commercially, not fixing problematic engines.
Many top equipment monitoring solutions provide these features to help your company with maintenance:
- Predictive engine and filter monitoring: Obtaining AI-powered actionable insights so you can predict maintenance and avoid emergency repairs instead of operating by a predetermined schedule is cost-effective and increases a business’ return on investment.
- Maintenance logging and reporting: Many top solutions include the ability to log and report your maintenance for leadership, as well as communicate with local maintenance businesses for easy-to-obtain services.
- Geolocation: With the ability to monitor both active and historical fleet visibility straight from phone or computer applications, location servicing has never been easier. Geolocation is perfect for theft prevention and keeping your aggregate equipment on-site.
- Driver workflows: Trucking operators can minimize guesswork and reduce paper-and-pen data entry with guided workflows and optimized productivity.
With both air and fuel filtration monitoring clearly showing as vital components to your average over-the-road fleet equipment, you will need to engage in this practice to keep up with your competitors.
In closing, just remember the biggest benefit of filtration monitoring is reducing unplanned and unwanted downtime. Keeping your vehicles on track to destinations without critical problems is key to being a fleet manager. Help yourself with predictive engine analytics by investing in digital maintenance tools that make your and your operators’ lives easier.
About the Author
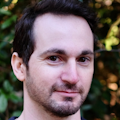
Chaz Vollmer
Product Owner | Senzit
Chaz Vollmer is an expert in data-driven technologies with over a decade of experience in product management and digital application design. As Product Owner at Senzit, he leads the user experience program and predictive analytics innovation team, focused on reducing heavy-duty equipment downtime.