In this article, you'll learn about:
- How to decide what filter change schedule is right for you
- How to use data to make sure you change your filters at the right time
- How to judge filter performance
For more on vehicle filters:
You may live by the mantra “Don’t Sweat the Small Stuff,” but for keeping commercial vehicles operating efficiently, the little things matter. That’s especially true when it comes to oil, air, and even cabin filters.
Employing best practices for filter changeout intervals during routine maintenance keeps costs low and trucks out of the shop for unscheduled repairs. But determining the most effective filter change intervals is an exercise that needs to rely on experience, data, and technology.
Across the board, fleets and filter manufacturers note that OEM filter change recommendations are based on what engineers who developed the system had determined to be most effective. Their requirements for filter changes also ensure warranty coverage.
Greg Treinen, vice president, on-highway market development at Daimler Truck North America, related that Detroit recommendations specify filter performance based on an optimum combination of filter micron rating and capacity, and mechanical requirements. The OEM also recommends filter maintenance intervals based on duty cycles that are grouped in four categories.
This includes:
- Efficient long-haul applications that average 7 miles per gallon or better
- Long-haul units with an average between 6 and 6.9 mpg and have minimal city stop-and-go operations
- Short-haul service for vehicles that travel 30,000 to 60,000 miles annually and average between 5.1 and 5.9 mpg
- Severe-service qualifications that apply to vehicles that travel up to 30,000 miles each year or average less than 5 mpg or that operate under severe conditions
Service data and even anecdotal evidence can also play key roles. Jay Stephenson, North American training supervisor for Fleetguard products at Atmus Filtration Technologies, for example, said it’s crucial to balance preventive maintenance schedules and service history. “Fleets should also check with drivers to gather feedback on any performance issues they may have noticed,” he added. “Drivers often spot issues before they become major problems.”
Gabriel Blevins, training manager at Donaldson, said while service history can be beneficial for optimizing uptime, sometimes maintenance schedules and practices are established and kept for long periods of time. “We recommend reviewing those practices periodically, as changes might have taken place with engine design and filtration technology,” he said. “Staying current is crucial to providing the best protection possible.”
In other cases, routine filter changes work best. For example, Donald Chilton, director of product management for WIX Filters, recommended changing cabin air filters at least once per year. “There is so much in the air that people don’t think about,” he advised. “A clean cabin filter allows you to have some defense against harmful contaminants.”
Cabin filters, which are typically changed annually, are important for maintaining healthy working environments for drivers, Stephenson noted. As such, these filters may need to be replaced more or less frequently, depending on the vehicle’s operating conditions.
Relying on data
Filter maintenance routines can be hard for fleets to change, noted Chilton. “Most fleets believe that if it’s working, don’t bother changing anything,” he said. “But we live in a world of data that can help make informed decisions. There is more available than ever, but some fleets don’t use it to their advantage.”
For Jerry Greiner, VP of business operations, procurement & fleet management at Transervice, oil sampling is one area where data can be helpful. “It can provide information about the condition of the oil at different mileage intervals,” he said. “The data from oil samples will show you the correct change interval and help determine PM schedules. This data is especially important if you want to extend oil drains.”
Some fleets stretch drain intervals by using oil analysis to detect early signs of damaging wear metals and identify contaminants, Chilton noted. “Oil analysis can alter routines,” he said, “but it requires a deep understanding of what the oil is doing and how much life is left as a result.”
Blevins advised having an analysis of new oil as a viscosity baseline. “This is important when looking at used oil samples,” he said. “When oil viscosity has changed considerably, it is time to take action.”
For oil and oil filter changes, Stephenson said, using telematics data can enable fleets to fine-tune their schedules or catch problems as they arise, such as coolant dilution or premature oil degradation. “For fleets with access to real-time telematics, performance-based adjustments may be possible, allowing for more precise scheduling of changes,” he added. “Data-driven maintenance schedules may also allow fleets to exceed standard service intervals when conditions are favorable.”
An onboard maintenance monitoring system in Detroit engines can compute optimal maintenance intervals based on the actual operating conditions, Treinen noted. The system utilizes powertrain data to determine specific maintenance intervals. “By honing maintenance recommendations based on engine and transmission load, the system reduces costs and downtime for service,” he said.
Real-time data can also come from technologies such as restriction indicators, Chilton related. “Air filters should be changed once the restriction gauge starts to signal the need for replacement,” he said. “Most air filter housings are already configured with restriction gauges, and retrofit kits are available for those that don’t.”
There are two key benefits to consider when servicing by restriction, according to Blevins. The first is that it can be common to get two or three times the life of the filter versus servicing at every oil drain interval.
“The other benefit is that the air filter becomes more efficient over time,” Blevins explained. “Once it develops a dust cake layer on the media, that dust attracts other dust very effectively, so letting the air filter stay in longer actually provides better engine protection.”
While air filters should be replaced at the precise time to avoid contaminating the engine with airborne debris (if changed prematurely) or restricting airflow to the engine (if changed too late), an air restriction gauge can help, Stephenson pointed out. “The good news about restriction gauges is they’re inexpensive,” he added. “And new and improved solutions can provide more reliable readouts on air filter service life.
Taking a closer look
“Overall, if you’re experiencing downtime or component failures, it’s critical to look at the filtration system you’re using,” Stephenson continued. “If your filters are not reaching their expected service intervals, it’s worth considering a change in brand or performance level after having a conversation with your filter supplier to better understand the cause of the issue. A practical way to evaluate the impact of filtration is to test different filters to see if a new filter improves vehicle performance.”
When considering filter changes, Greiner noted, account for the environment the truck is operating in and its duty cycle. “Start with a pilot on a set number of trucks that have similar duty cycles to get comparable results,” he advised.
It’s important to note, according to Treinen, that finer filtration generally provides increased engine service life, but may require shorter filter change intervals. “When selecting your filter, be sure to choose one that meets SAE standards,” he said. “It is also important to note that capacity and efficiency ratings should not be the only criteria on which to judge filter performance. Other factors, including media strength, resistance to impulse failures, and burst strength often differ greatly between filter makes and should be considered in the filter selection process.”
No matter what brand you choose, Blevins said to start with premium OE grade filters. “If that baseline is met and problems arise, it’s important to determine what the problem is before changing,” he added. “Treat each situation with an investigative approach. If you are looking to change filtration away from OE recommendations, there are risks involved, and caution should be taken.”
“Changing brands is always more complex than it initially appears,” Chilton said. “If you are not happy with the results of your current filter, do your research and find the brand that works for you. Nothing beats good maintenance software and faithfully logging data. If you’re diligent, this is by far the best investment you can make.”
For Stephenson, the key to determining the optimal service schedule for a truck’s filters is to find the “Goldilocks Zone”—not changing parts too early or too late to maximize their lifespan and system protection as well as reduce unnecessary maintenance costs.
“Higher-quality filters, like many other components, usually offer longer service intervals and can be worth it,” Stephenson said. “Saving a buck or two on filters could cost you more in the long run if it impacts vehicle performance and lifespan.”
About the Author
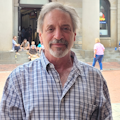
Seth Skydel
Seth Skydel, a veteran industry editor, has more than 36 years of experience in fleet management, trucking, and transportation and logistics publications. Today, in editorial and marketing roles, he writes about fleet, service, and transportation management, vehicle and information technology, and industry trends and issues.