Every stop. Up and down, down and up. Day in and day out. That’s the life of a liftgate. And it’s hard to imagine that pickup and delivery duty cycles—and so many other operations—could function effectively without these mechanized lifts. But who really thinks about liftgates and the heavy burden placed upon them? Not many, unless they stop doing their job.
A malfunction can be caused by many components. While a liftgate’s job—raising and lowering the loading platform—is simple, it takes a complex partnership of mechanical, electrical, and hydraulic systems. Issues can arise from any of these areas. A drained battery, corroded wire, or a torn hose can all lead to downtime. (All good reasons to emphasize inspections and preventive maintenance.) And being located at the back of the truck means a rear-end collision can also take the elevator out of action.
Because there are so many maintenance considerations, we asked experts to weigh in on liftgate best practices. They range from liftgate and truck body manufacturers to dealers and service providers, and all have one thing in common: They do actually think about liftgates a lot.
Our panel includes:
- Arnold Kowal, Director, after sales service support, Maxon Lift
- Robert Tonon VP of technical services, Waltco
- Chris Parsons, Director of branch operations, Great Dane
- Ryan Fisher, Director, dealership service operations, Bentley Truck Services
- Cristian Fonseca Box/trailer shop manager, Fleet Fast
[The following was lightly edited for style and clarity.]
Fleet Maintenance: What are some common and uncommon liftgate problems?
Robert Tonon: Electrical issues are typically number one. The two most common problems are switches and motor solenoids, followed closely by electric motors. Hydraulic problems, such as valves and coils not functioning properly, are second. To a smaller extent these days, unless there is a specific batch problem, leaking cylinders are second to valves and coils.
One area that is not common, found on heavy-use or older products, is simple pin or bushing wear. Left to fester, that can become a safety issue. This is an area where the attitude of “if it’s not broken, I don’t need to fix it” comes into play. Ultimately, it can compromise the life of the liftgate if not addressed in a timely manner, because the cost of repair becomes too expensive, and it’s no longer worth it.
Ryan Fisher: Common issues we have found are related to platform alignment and lighting failures caused by body builder modifications, so it’s important to inspect for those before putting the vehicle in service. We’ve also seen leaks in hydraulic hoses or cylinders, so we double-check the tightness of fittings and hardware and top off hydraulic fluid levels.
Especially in corrosive environments in the North caused by road salt, there are electrical issues with connections and some switch failures. Failing to properly grease fittings on a regular basis will also wear out bearings, bushings, or pivot points, and we have some platform misalignment issues that can cause difficulty in opening or closing.
Read more: Liftgate PM planning
Fatigue caused by overloading is a less common issue caused by lack of user maintenance. Pump or motor failures occur less than 5% of the time.
Recommended tools for liftgate service and repair
- Multimeter for voltage and ohms testing and to diagnose electrical problems
- High-amp DC induction ammeter for testing charge systems and amperage draw
- Pressure gauge to test pump and verify lift works efficiently
- Hand tools that include wrenches, screwdrivers, hammers, pliers, side cutters, crimpers for both large battery cables and smaller gauge wire
- Hydraulic test gauges to verify sufficient system pressure to lift a given load and to determine if blockage or leaks exist
- Digital volt-ohm meter to measure voltage, current, resistance, and if a particular circuit has continuity or is open
- Battery tester to measure voltage, current, and resistance under different conditions and identifies weak or failing batteries
Other:
- Grease gun
- Electric tools with solder, heat shrink, etc.
- Safety glasses and gloves
- Torque wrench
- Small spill kit for fluid leaks or loss during maintenance
- Small propane torch
- Jack stands
Arnold Kowal: The most common liftgate repairs are associated with either control switches or electric motor solenoids.
There are fewer repairs associated with replacement of metal components due to corrosion from exposure , de-icing agents, and the environment. Most manufacturers have adopted new processes for better corrosion protection, such as galvanizing or e-coating. They also use alternative materials such as aluminum, stainless steel, or polycarbonates.
Cristian Fonseca: Frequent concerns include hydraulic issues such as leaks, pump malfunctions, or cylinder problems, as well as electrical faults caused by issues with switches, wiring, and batteries.
Less common issues, typically from accidents, include advanced control system malfunctions and major structural damage.
Chris Parsons: Most common are hydraulic line and fitting ruptures, and electric solenoid, wiring, switch and charging issues. There are also problems with platform linkages and chains on rail lifts.
FM: How often do liftgates require inspections and preventive maintenance?
Fisher: Proactive maintenance is the key to extending the frequency of repairs. Operators should perform daily visual inspections before using the liftgate, and check for any visible damage, loose or missing bolts, and signs of hydraulic fluid leaks. They should also ensure that safety features such as warning lights and alarms are functional.
For regular PMs, operators should refer to product documentation provided by the liftgate manufacturer for specific requirements. At Bentley Truck Services, [an authorized service center for Isuzu, Hino, Mitsubishi Fuso, UD Trucks], we clean and grease gates at 10,000 or 15,000 miles depending on engine oil change intervals. We also perform either four- or six-month full liftgate PMs that take around two hours. Those include cleaning all connections and replacing any in the electrical or hydraulic systems that require it. The PM includes a full load test for proper operation and speed as well.
Fonseca: Service frequency varies, but hydraulic and electrical systems often require more attention. Regular inspections, ideally monthly, are recommended, especially for high-use liftgates.
Read more: In search of a smooth ride: Image examples of suspension wear and damage
Tonon: Frequency is usually not scheduled specifically for liftgate maintenance but rather follows the maintenance schedule of the truck or trailer, which could be every three months to as little as once a year.
Kowal: Operators should do a daily pre-trip inspection to look for physical damage, ensure operation of liftgate latching components for transit, ensure there are no unusual sounds coming from the liftgate motor enclosure, and verify all functions of the liftgate operation are working properly.
FM: When liftgates stop working, what are some troubleshooting best practices?
Fonseca: Troubleshooting best practices begin with an initial inspection for visible damage or wear and operational testing to ensure the liftgate functions correctly. A hydraulic system evaluation should check for leaks and assess pressure, and an electrical system check should include the battery, wiring, and switches.
Overall, always refer to the manufacturer’s troubleshooting recommendations.
Tonon: First, diagnose the problem. Don’t guess or needlessly change parts. Most tests are simple using a multimeter. In some cases, a pressure gauge is also useful.
Waltco offers a tool that can be accessed on a phone, tablet, or laptop that asks questions, and your answers direct you to the next step until you reach a diagnosis. It also provides the part number and ordering information. If the problem can’t be solved using the tool, it leads you to a phone number that you can call and speak to a technical support person.
Fisher: Begin with confirming and verifying the customer’s complaint by conducting a visual inspection of the liftgate and its components. It’s also important to review the load capacity to be sure the liftgate is being used within spec. Diagnostics can then begin and so should inspections of hydraulics for fluid leaks around hoses, cylinders and connections, and electrical systems, including power sources, grounds, relays, and switches.
Kowal: In general, when troubleshooting any issue, you want to start at the source that provides power to the liftgate motor. This means checking the state of charge of the battery pack and/or the charging system.
If you are not using a hydraulic test gauge when troubleshooting a hydraulic system issue, you are essentially working blind. The pressure gauge provides visibility to technicians and allows them to determine such things as if the hydraulic pump is producing sufficient system pressure to lift a given load or if there is a blockage or leak in each circuit. It is always important to ensure you are using the correct scale of pressure gauge. The gauge should be operated at pressures that do not normally exceed 75% of the full scale of the gauge.
FM: In the event of a collision, what should technicians focus on when inspecting liftgates?
Parsons: Look for any bent or broken runner columns or arms and for major leaks. Check all pins and bushings, as well as rollers and the platform for damage.
Kowal: Technicians should be cautious of physical damage to liftgate components that may not always be obvious but can lead to binding of the liftgate geometry, which in turn leads to accelerated wear and tear of other components. Many times, these issues don’t show up until after you get the gate operational.
Fonseca: A post-collision liftgate inspection focus should include a structural assessment to look for any signs of damage, functional testing to ensure smooth operation and correct alignment, system checks to examine hydraulic and electrical components, and confirmation that all safety features are operational.
Tonon: Once the repair of physical damage is complete, the best practice would be to do a thorough test that involves making sure cycle times, pressures, and voltages are all within guidelines.
If any of these are not meeting the normal standard of good operation, it indicates something was missed in the repair.
About the Author
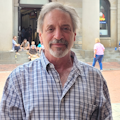
Seth Skydel
Seth Skydel, a veteran industry editor, has more than 36 years of experience in fleet management, trucking, and transportation and logistics publications. Today, in editorial and marketing roles, he writes about fleet, service, and transportation management, vehicle and information technology, and industry trends and issues.