The role of composites in heavy duty trucks
Composites have long been used in the construction of heavy duty trucks and trailers. The primary benefits of using such materials are clear: reduce weight and thereby improve fuel economy and cargo-carrying capacity.
“Composite materials are used in many locations on heavy duty trucks,” says Jim Nachtman, director of heavy duty marketing for Navistar, a holding company whose brands include international trucks. “Examples include hoods, bumpers, skirts, cab extenders, and roof air fairings, as well as many interior components such as cabinets and the instrument panel. Engine components such as the International A26 engine valve cover, oil filter cap, and fuel filter cap are composite as well.”
In addition to weight savings, Nachtman says composites provide benefits including lower replacement parts cost and enhanced flexibility for certain applications such as bumpers. Given all of these benefits, some wonder if the use of composites could be expanded in the coming years.
“Look at the Boeing 787 airplane,” says Rich Schiavoni, head of Academy Training for Wurth USA, a supplier of vehicle services, parts, and products. “It is primarily composite, so it is certainly possible. A carbon fiber chassis on a heavy duty truck? I’m not sure. I don’t know how much carbon fiber flexes, but I would think that everything bolted to the chassis and above, excluding the drivetrain, could go away from steel. The same goes for trailers. What holds the weight needs to be extremely strong, but what keeps the weight in has more options.”
Some who have been entrenched in the heavy duty collision repair industry aren’t so sure the use of composites will increase.
“I don’t think we’ll ever see composites with a frame, at least not in my lifetime, and I’m 60,” says John Spoto, national heavy duty commercial manager for the automotive aftermarket division of 3M, a maker of abrasives, adhesives, and coatings for auto body repair. “Just look at what has happened on the auto side. The auto side isn’t even there yet.” Spoto is also an instructor for I-CAR, the Inter-Industry Conference on Auto Collision Repair.
Despite the justifiable naysaying, an Iowa-based bus manufacturer is proving that composites can play a more pivotal role in the construction of large vehicles.
“A company called Proterra is using composites to make electric buses,” says Michael Hoke, president of Abaris Training, a Nevada-based organization that has been providing advanced composite training since 1983. “One of our instructors taught a damage repair class in Toronto the first week of January because Proterra has a fleet of buses there. We’ve actually done quite a few of these classes for Proterra over the past few years.”
Proterra is using both carbon fiber and fiberglass in its electric buses, materials that are used based on design and loading requirements.
“One of the primary advantages of composite construction is the ability to vary the makeup of materials throughout the vehicle,” says Mike Finnern, Proterra’s vice president of customer service. “This allows for a design optimized for strength, weight, and durability.”
According to Finnern, the utilization of composite materials has allowed Proterra to remove 4,000 lbs of weight compared to a traditional metal bus frame and chassis. “The primary advantage for an electric bus is that it can now store more energy [batteries] onboard to extend its range,” Finnern points out.
Abaris Training has also been engaged by a leading manufacturer of semi-trailers. “We’ve had some personnel from Wabash National come through our training facility,” Hoke says. “Wabash is using composites in refrigerated trailers because composites can be good insulators.”
Wabash National is using a unique molded structural composite (MSC) technology, an advanced material consisting of a high-efficiency foam core that is encapsulated in a polymer-reinforced shell and protective gel coat. Robert Lane, vice president of product innovation, says MSC not only reduces weight and eliminates corrosion, but also provides twice the puncture resistance while also improving thermal efficiency by up to 25 percent in 53’ van applications. Wabash is also using MSC in its truck bodies.
Material selection and the fleet’s ROI
Regardless of what type of material a manufacturer chooses to use — composite, steel, aluminum, or otherwise — Navistar’s Nachtman says the selection is typically based on several factors including strength requirements for the application, cost, serviceability, paintability, weight, temperature, and corrosion.
Volvo Trucks, for example, is using a variety of composite materials including plastic and carbon fiber.
“It’s the partnerships with our suppliers that help us determine which type of material should be used,” says Chris Stadler, product marketing manager at Volvo Trucks North America, which offers a full range of medium to heavy duty trucks. “We make sure the materials used address the best fit, form, and functionality. We also use different materials to enhance the aesthetics of the truck and investigate composites that could improve the value of the vehicle such as the costs and weight of the components. Testing and validation on these materials is always being performed. We will not sacrifice the safety, quality, and integrity of our products.”
Case in point, Volvo Trucks incorporates a high-strength steel cab because the company’s core value is safety. “We want to keep our customers and their drivers as safe as possible,” Stadler adds.
For tractor-trailer manufacturers and the fleets they serve, cost-benefit analysis is key.
“When you think about the upfront cost of a vehicle, steel is more cost-effective than aluminum, magnesium, and reinforced composites,” says Jody Hall, vice president of the automotive aftermarket for the American Iron and Steel Institute (AISI).
For fleets in long-haul or linehaul applications, however, where fuel efficiency and cargo-carrying capacity are paramount, the added upfront cost could be offset by longer-term fuel savings and productivity gains.
There is no disputing the fact that composites are lighter weight. However, Hall says recent advances in steel are offsetting some of that advantage. “Over the past four years, steel strength has been increased 10 times,” Hall points out. “Because of that increased strength, we can reduce thickness. That is how we’re able to achieve light-weighting.”
Regardless of the degree to which composites are used in heavy duty trucks, it’s important for technicians to understand what composites are and how they differ from materials such as steel and aluminum.
“Any composite is basically a fiber-reinforced resin system,” Abaris Training’s Hoke explains. “You can have either glass, carbon, or Kevlar fibers.”
In the automotive industry, Hoke says the most common composite is fiberglass. Fiberglass is the least expensive of the three; carbon fiber can actually cost up to 10 times as much as fiberglass. Fiberglass is also quite effective at resisting impact damage. “The only real disadvantage is that fiberglass is heavier than carbon fiber, though it is still considerably lighter than steel,” Hoke points out.
One might jump to the conclusion that because they are lighter weight, composites must lack strength and durability. As Hoke points out, this is not the case — if the composites are engineered correctly. As an example, he points to the Formula 1 race car. “It is almost entirely constructed of composite materials,” Hoke says. The result is a lightweight vehicle that is still capable of withstanding violent crashes.
Hoke also points to an incident in Texas, where a Proterra electric bus was T-boned by a concrete mixer. “The collision crushed in the side of the bus to a certain extent, but not as badly as you’d think it would have,” Hoke says. “The bus was actually able to drive away after that, and all passengers walked away too. You can make composites extremely crash-worthy if you design properly for it.”
That said, any damage incurred is still going to need to be repaired.
Best practices for repairing composites
Hoke says technicians will largely be able to rely on existing auto body tools and techniques to make composite repairs. However, there are some differences to be aware of, such as cross-contamination.
“Whenever you put carbon fiber composites directly against steel or aluminum, like if you bolted a steel or aluminum door handle to a carbon fiber door panel, the carbon fiber will cause the steel or aluminum to corrode,” Hoke says. “It’s a galvanic corrosion problem. It doesn’t hurt the carbon fiber at all but will attack the steel or aluminum. So, you need an insulator between the two to prevent that corrosion.”
Fiberglass, on the other hand, will not cause that kind of galvanic corrosion. That is why Hoke thinks fiberglass will ultimately emerge as the preferred choice when it comes to composite materials in heavy duty trucks. Fiberglass is also fairly straightforward for technicians to work with. “You can typically drill holes in it with traditional tools,” Hoke says. “That is not true with carbon fiber where technicians need different [drill] bits.”
Hoke believes the heavy duty truck industry has an advantage when it comes to repairing composites. “In the airplane world where we mostly use carbon fibers, we see a lot of adhesively bonded repairs,” Hoke relates. “For instance, a puncture or dent would be bonded, and then it would have to be cured for a couple of hours at a fairly high temperature of 180 to 350 degrees F. That can be time-consuming and a little tricky to set up.”
Conversely, in heavy duty trucks where Hoke envisions more fiberglass composites, the repair process could be much simpler.
“With fiberglass, a technician can consider doing a ‘bolted doubler’ repair,” Hoke says. “If a hole is punched in the side of a trailer, for example, the technician could cut another piece of fiberglass as an external doubler, drill a few holes, and then bolt that doubler over the hole. It won’t necessarily look very pretty, but it would work.”
Whether working with fiberglass or carbon fiber, some in the vehicle collision repair business lean toward a different approach to repairs.
“While CFRP [carbon fiber-reinforced plastic] is a newer material, it still acts like FRP [fiberglass reinforced plastic] and may, in fact, be repaired the same way,” says Doug Craig, Fusor field technical support and training manager. Fusor, a brand of Lord Corp., is a line of adhesives and coatings.
Craig says technicians can follow a standard repair process. “Technicians could use our 100EZ plastic repair adhesive, which is a heat-set epoxy, along with our cloth or any kind of glass or carbon fiber cloth,” Craig says. The cloth is used to duplicate the amount of fiber in the panel. The adhesive is used to hold the cloth and entire repair area together.
For example, a rock is tossed into the air and puts a hole in a fender. The technician should first taper things out on the edge of that hole, followed by building up the patch. The technician also wants to have a lot of “grab” to the existing base material. Craig shares in detail how this can be done.
“You want one layer of backside reinforcement that is larger than the hole,” Craig points out. That reinforcement material then needs to be cured. Then, the technician can start working on the frontside of the repair by applying layers of adhesive cloth until enough has been built up to duplicate the panel thickness. “At this point, you start rolling it down to get the air out of it,” Craig explains. “Then we do another heating [curing] to lock things up.”
The heating steps are very important and should be followed precisely by technicians. Epoxies will generally harden in minutes or hours depending on the product and certain environmental factors. Additionally, depending on the epoxy, it may continue curing for a period of time after the heat source is removed.
“As it cures, the epoxy can change in size ever so slightly,” Craig says. “That’s what can give you ghosting or read-through. You still have a strong repair, but you can see it. Some fleets might not care, though.” If the fleet does care, technicians need to be aware of this potential addition to curing time.
Even before this multi-step repair procedure takes place, 3M’s Spoto says one of the biggest things technicians need to keep in mind is cleaning. Anytime a composite material is hit, it creates a fracturing effect. “That’s why it is so important for technicians to make sure the surface is clean before they begin to sand,” Spoto says.
It is also essential to keep the cleaning solvent away from the fractured areas where fibers are exposed. “If the technician oversaturates the surface with cleaning solvent, the solvent wicks down in,” Spoto explains. “When the technician completes the repair and repaints it, it looks great. But later on, mapping can set in.” Mapping refers to repairs where improper preparation results in the repair area showing through the basecoat and clearcoat.
In addition to proper cleaning of the repair area, Spoto says it’s critical to provide proper support to the repair area. He likens it to a broken arm, where the doctor wants to support the structure on all sides.
“When repairing a composite panel, you must support the backside in order to give support to the frontside,” Spoto says. “When the backside is properly supported, repairing the frontside is easy.”
Another thing technicians need to think about is the variety of materials they may run into simultaneously when making repairs. As Wurth USA’s Schiavoni reminds, technicians may run into a heavy steel chassis and driveline, an aluminum structural internal, and composite coatings. This creates a situation where technicians may need to adapt their normal practices, as well as the tools they reach for in their toolboxes.
“With the inner structure, technicians in the old days could spotweld all of the panels together when reassembling,” Schiavoni says. “Now you’re having aluminum panels adhere to steel inner panels and then a plastic panel over the top. You can’t weld aluminum to stainless steel; you have to glue it and use self-piercing rivets which essentially stitches the vehicle back together. So, technicians need a good self-piercing riveting tool, as well as a good structural adhesive.”
According to Lord Corp.’s Craig, a fleet maintenance shop already involved in body repair should have most of the tools it needs to tackle composites. One unique item would be a fiberglass roller so technicians can roll the air out of the fabric and get any glass thoroughly mixed with the adhesive. Technicians will also need a good heat source, typically a paint-curing lamp. They also need some kind of applicator for the adhesive cartridge which could be manual, electric, or pneumatic depending on preference.
Speaking of adhesives, technicians should make sure that what they are using is designed for the material they are repairing.
Spoto says 3M recommends a urethane two-part component or an epoxy to the backside, and an epoxy to the frontside. “We’ve done a lot of comparisons with polyester resin,” Spoto points out. “Fiberglass polyester resin won’t work on SMC (sheet molding compound). You have to use SMC resin for SMC or it won’t stick.” SMC is a ready-to-mold, glass-fiber-reinforced polyester composite material primarily used in compression molding.
Craig says the 100EZ plastic repair adhesive from Fusor has a hardness that is on par with SMC, fiberglass, and carbon fiber.
“I am shocked that I still see heavy duty shops that mix fiberglass resin and hardener to fix SMC hoods,” Craig relates. “The hood gets into the paint shop and they just want it out, and the vehicle owner just wants the truck back on the road. So, the hole is filled up and they call it good enough. But that’s not what I would call a quality repair that is to pre-damage condition. It will last a while but will not last as long as if the technician had used the right epoxy.”
As the use of composites in heavy duty vehicles persists, fleets can also look to their service partners for help.
“Most components in need of repair, no matter what the material, should be repaired or replaced through the dealer,” Volvo Trucks’ Stadler says. “Most composites are designed for a specific purpose and the servicing of those parts should be taken into consideration. The type of material and design of the part will determine whether they can be repaired or replaced by the fleets. Volvo Trucks North America provides the necessary instructions to our customers for the components they can repair or replace on the vehicle.”
Regardless of material makeup, the question of “repair versus replace” is something all fleets will always wrestle with. With the right training, tools, and materials, the opportunity to repair composites might prove to be a cost-effective option more often than not.
About the Author
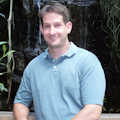
Gregg Wartgow
Gregg Wartgow is a freelancer who Fleet Maintenance has relied upon for many years, writing about virtually any trucking topic. He lives in Brodhead, Wisconsin.