Tool Briefing: How to diagnose different suspension noise issues
Vehicles Affected:
- 2007 Toyota Rav4
- 2004 Mercedes Benz S430
- 2001 Peterbilt 379
Diagnostic Tools Used:
- TSBs
- Vehicle specification chart
- Tape measure
- Four-post lift
- LED lighting
- Floor jack
- Jack stands
- Pry bar
- Dial indicator
- Temperature gun or probe
- Digital multimeter/GoPro camera
- Smart Ear
The source of suspension or steering noises can be difficult to locate because sound may travel along metal parts and make it seem as though one component is at fault, while the noise is actually originating from an entirely different area. It is also likely a noise will be intermittent and difficult to duplicate. In this month’s article, we will look at some suspension noises, and the tools and practices used to determine the source of the noises.
Step 1: Determine the conditions that cause the noise
When determining the cause of a customer concern, a technician needs to obtain enough information to understand what and when an issue occurs. This is extremely important with noises because many factors contribute to the ability to duplicate the noise. In some cases, just the simple fact of the load in the vehicle, such as the number and size of passengers or cargo, can either change or eliminate a noise. It is also possible that a person, who is used to driving a particular vehicle, may not notice a noise that a technician readily hears. The technician may assume it is the cause of the customer’s concern, and could repair something that does not “fix” the vehicle.
Ask questions of the driver of the vehicle, not necessarily the person that brought the vehicle in for service. Questions to the driver will provide the correct information as to when, how and what noise is of concern. One of the things you need to do is figure out what type of noise the vehicle is making. A “creak” or “groan" or “snap” is typically caused by a worn bushing or component caused when two metals objects rub against each other. A “growl” or “whine” can be caused by a worn bearing or tire. Once you have that information and can duplicate the noise, the diagnostic work can begin.
Step 2: Visual inspection of suspension and steering systems
Prior to the start of your visual inspection, use your repair information source to look up the vehicle specifications, paying attention to items that you would not normally consider such as ride height. If there are worn components that are causing a noise, there could be wear that is also causing changes in ride height, and having that information could assist in the diagnosis.
Use a tape measure and accurately check both sides of the vehicle in the front and rear to verify the vehicle height is at the proper specification. If the ride height is incorrect, look at struts, springs and their mounts a little closer to make sure there are no issues. Repair any worn items to restore the correct ride height. Additional repair information could include TSBs, alignment specifications and tolerances for suspension and steering components like ball joints or tie rods.
The tools you will use to diagnose a noise are determined by the type of noises, as well as when the noise occurs. A thorough inspection of the chassis and suspension is necessary with all noises. A well-lit area and a lift that keeps the suspension “loaded” with the tires on the lift are preferred, but a lift that allows the wheels to “hang” also can be used.
If you do not have a four-post or alignment lift, a lift that allows the wheels to hang may be used to perform the visual inspection of the frame, mounts, steering and some of the suspension components. It will be necessary to load the suspension at some point to evaluate the ball joints and struts to make sure that any movement is within the manufacturer’s specifications. This can be accomplished by using a floor jack and jack stands to raise and suspend the lower control arm, while lifting a pry bar placed under the front tire to check for excessive movement of the ball joints and strut mounts. In some cases, there is an acceptable amount of movement. To determine this, use a dial indicator placed on the control arm and compare the movement to the specifications from the vehicle manufacturer.
I like a well-lit area because shadows under the vehicle can hide issues that may be causing the noise. Some lifts include attached lighting systems directly on the unit. If your lift doesn't include these options, a worklight or flashlight with good illumination works as well. A four-post lift that keeps the wheels loaded to the ground will allow you to observe the suspension with the weight of the vehicle on it and may show that bushings or components are moving out of position when there is a load on them rather than hanging. An alignment lift that allows turning of the wheels also will provide an opportunity to observe the suspension under a load in more positions than straight ahead.
Step 3: Diagnose the noise
Once your visual inspection is complete, and you have determined that there are no components that are visibly worn, it is time to check for other potential causes of a noise. A technician sometimes needs to be creative in how they diagnose a vehicle, especially when an intermittent issue occurs. Creativity can be used in both how you cause the noise to occur as well as how you determine the cause. One of the items we have found useful is a temperature gun or probe connected to your digital multimeter.
Since friction creates heat, a rise in temperature is a clear indicator of an issue. As an example, if you have a whining noise after road testing the vehicle, use your temperature gun to measure the temperature of each wheel hub to determine if one side is hotter than the other. If they are the same temperature the noise could be caused by a tire. If they are different, the noise is likely due to a faulty hub bearing.
This method was recently used to determine the noise that was causing a “growl” from the front of a 2007 Toyota Rav4. Temperature testing also could be used to determine if a strut is working properly.
Because compression of the gases within a strut will cause pressures to increase, the temperatures of the strut also will rise. Using your temperature gun, you should see an equal rise in temperature from side to side of the vehicle. If temperatures are not the same, it could indicate that there is excessive movement in the suspension on one side or there is a problem with the strut.
We also had a Class 8 Peterbilt truck that was making an unusual noise and riding extremely rough only when turning right over any dip or bump in the road. We suspected that there was an issue of the suspension binding, causing the suspension to “snap” when the load became so great that it needed to release. Using our creative side, we placed a pair of dial indicators on each side of the rear air suspension and placed a GoPro camera near them to monitor the movement of the dial indicators. During the drive, we noticed that there was substantially less movement in the right side suspension, which we determined to be caused by a faulty airbag. Once the airbag was replaced, the noise was gone.
Noises that “travel” can be the most challenging to diagnose. Let’s say you have a faulty lower ball joint. The “pop” or “snapping” noise that is created will travel through the entire suspension, making it difficult to determine the root cause. The noise may sound as if it is coming from the strut mount, or even the upper control arm.
In order to determine the cause, one of the most useful tools we have used is the Steelman Smart Ear. This tool uses a series of clamped wireless transmitters that are attached to various vehicle components, and a receiver that the technician can use to listen to the noises generated by those components.
For example, you could clamp the transmitter to the strut mount, upper control arm, lower control arm and the body of a vehicle. The noise that is heard through the receiver will be loudest at the individual component where the noise originates.
We recently used this tool to diagnose the cause of suspension noises on a 2004 Mercedes S430. Listening to the noise without the Smart Ear, it was nearly impossible to determine which component was causing the issue. Even though there was noise coming from the transmitters connected to both the upper and lower control arms, it was noticeably louder from the upper control arm, indicating an issue with that component.
Step 4: Complete the repair
When performing repairs, you need to consider a few things that are common errors some technicians make that can cause component failures down the road. One thing some technicians do is to use a hammer to hit suspension parts, such as a control arm, to break the ball and socket loose from the control arm. Hitting the control arm may cause the socket to become oblong where the ball joint seats, causing the joint to not seat fully and fail prematurely.
Using tools designed to break the joint loose, such as the OTC 6297 Ball Joint Remover, without causing other component damage will avoid potential issues.
In many areas of the country rust and corrosion will make it extremely difficult to remove or adjust steering and suspension components. Fortunately, my shop is in California where we do not see rust very often. But when we do, we have found that the Knipex Swedish Pipe Wrench will grip the rusted parts, such as the tie rod sleeve in the photo, allowing the technician to remove or adjust the sleeve much easier.
Another thing I have seen many technicians do is re-use locking nuts on suspension and steering components. Most of the self-locking nuts (not utilizing a castle nut with a cotter pin) used on steering components are intended to be used only once, so you need to replace them. You can think of them like a cylinder head bolt, use it once because they have been stretched and cannot tighten and remain tight properly.
After you perform the repairs (see sidebar for the tools used to replace the control arm and hub bearings), it is imperative to perform the road test and diagnostic tests again in the same manner that originally duplicated the noise to assure a complete repair has been done.
About the Author
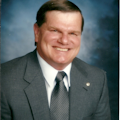
Barry Hoyland
Barry Hoyland has been in the independent aftermarket for more than 45 years as a technician, technician instructor, shop owner and shop management consultant. He owned and operated a successful Southern California automotive repair center that offers complete auto care and specialized in emission and diagnostic services for over 28 years. Hoyland also owned a company that modified vehicles to perform as emergency response units and mobile command centers, incorporating high-end electronic components into today’s vehicles. Barry has experience with all size and types of vehicles including traditional gas, hybrid electric, alternative fuel, and heavy duty diesel trucks.
Hoyland has provided consulting services for many automotive shops, fleets, and government agencies in order to improve their operational efficiencies.
In addition, Barry has worked with many NHRA drag racing teams as a crew chief on supercharged alcohol and nitro-methane fueled cars and currently serves as a crew chief on an Top Alcohol Funny Car, A Nostalgia Funny Car and a Nostalgia Alcohol Dragster
Hoyland holds certifications in ASE: A1, A6, A8 and L1, MACS 609, maintains a California Advanced Emission license, and a CDL with endorsements for double and triple trailers, tankers, and HazMat.
When he is not helping to run a shop in the Pacific Northwest, Hoyland travels across the U.S. as an instructor of technical and shop management courses, many of which he has developed.