For maintenance shops and technicians to save time, produce superior work and boost productivity, it is imperative that they have the appropriate tools, tool storage solutions and shop equipment.
Manufacturers design tools and shop equipment for specific applications, and they should be used only for those intended purposes. When a shop or technician doesn’t have the necessary tools/equipment, and the wrong one is used instead, vehicle maintenance and repair can be frustrating, as well as inefficient. That results in lost productivity from slower work and more errors.
Using the wrong tool or shop equipment also increases the risk associated with its use. It can make the work dangerous for technicians and could result in an injury. What’s more, the tool/shop equipment and/or the vehicle or component being worked on also could be damaged.
All of this increases the risks for accidents. Accidents cause downtime. That impacts job and shop productivity.
BEST PRACTICES
It is always wise to invest in superior, well-designed, high-quality tools and shop equipment. This will:
- Make the technician’s job safer and easier.
- Improve the quality of the work being done.
- Help extend the life of the tool/equipment.
Even when a shop has the appropriate tools and shop equipment, technicians need to understand the importance of the selection and use of those tools/equipment to do a particular job safely. That includes:
- Using the appropriate personal protective equipment (PPE).
- Staying current on safety techniques.
- Following safe operating practices.
There are occasions when technicians feel that taking the time to get the proper tool/shop equipment to complete a job will slow down their work. Sometimes, technicians figure it doesn’t hurt to improvise with a tool/equipment once in a while.
That being the case, it is advisable for shop managers to regularly remind their technicians that improvising with the wrong tool/shop equipment can result in work of poor quality. Worse, injuries and property damage can occur when a technician is in a hurry and substitutes what is convenient for the proper tool/equipment.
Not to be overlooked is the importance of regularly inspecting, maintaining and servicing tools and shop equipment to keep them in optimum, safe and reliable working condition. This helps them last as long as possible.
Any defects and/or safety problems found need to be corrected before they become a serious hazard. A defective tool or piece of shop equipment should never be used. It should immediately be replaced or be taken out of service until it has been repaired.
ORGANIZATION
Proper organization and storage of tools and shop equipment is also essential to helping them remain in good condition for a long time. Furthermore, technician and shop productivity is increased when tools/equipment are easy to find, available and ready to use when needed. Time is not lost looking for them.
The time technicians spend off a job when searching for a lost tool, or a tool required to complete a job, can add up quickly in job delays, reduced work efficiency and increased expenses.
In addition, costs are reduced because tools/shop equipment are less likely to be lost, damaged or stolen and will not have to be replaced.
A best practice is to have suitable fixtures with marked locations to provide orderly arrangement of tools/shop equipment. Remind technicians to return tools/equipment promptly after use.
Not only does this reduce the chance of their being misplaced or lost, it can help prevent accidents because if tools/equipment are left or placed in an incorrect area, there is a possibility that someone could slip or trip over them.
About the Author
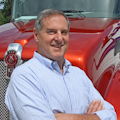