Mitchell 1 enhances TruckSeries with tools to boost productivity and efficiency
ORLANDO, Florida—Mitchell 1 debuted an update to the TruckSeries repair information platform featuring two new digital tools to help commercial vehicle technicians at American Trucking Associations’ Technology & Maintenance Council 2022 Annual Meeting & Transportation Technology Exhibition. The first is a time management tool to bolster shop productivity and the second an improved wiring diagram tool to assist with electrical diagnostics and repairs.
Both features added to Manager SE Truck Series software, which is used to help service Classes 4-8 trucks, were developed to help technicians work smarter and more efficiently as the transportation industry becomes more complex and high tech, according to Ben Johnson, Mitchell 1 director of product management.
These advancements include more efficient advanced driver assistance systems (ADAS), diesel engines, electric drivetrains, and autonomous trucks.
“With these new technologies, maintenance technicians will experience a lot of ‘first time’ events in the repair shop with no experience to draw upon,” Johnson said. “What this means is that techs on the front lines will need to adopt a proven electronic diagnostics strategy to succeed in repairing and maintaining fleets with these advanced technologies.”
Wired Up
The Advanced Interactive Wiring Diagrams update addresses a way to more quickly resolve issues within the truck’s electrical systems. Now technicians can search for and identify connectors, grounds, and splices in a more interactive way.
Other improvements include a dropdown history that shows the previous 10 diagrams viewed in a session.
The exclusive feature allows a technician to navigate via the diagram directly to repair information for components. The component names are hyperlinked to the information a tech needs, such as location, connector views, and replacement procedures.
Johnson demoed the display, where he went through how to locate a fuel rail pressure sensor wiring diagram on a Cummins X15 engine. The wiring diagram for that part was highlighted in yellow for better tracking.
“As a technician, I can very quickly focus in on what I want to see. I can dim the rest of the wires so that I can focus even better,” Johnson explained. “Now I can zoom in and see what I'm interested in looking at.”
Prompts also give warnings, such as that the fuel is under high pressure and that the fluid is hot and could cause burns. Parts and repair information are displayed. The feature also works in conjunction with diagnostic tools such as a multimeter or digital oscilloscope.
Johnson said this is vastly different than the old days of Mitchell’s thick brown books, where a tech would bookmark a page, find additional information about the sensor somewhere else, and then continue on the task. Digital diagrams also had efficiency issues.
“I [would] exit the diagram, search for the sensor, find out what I want to find out about it, come back in to research the diagram, and then go to the next step,” Johnson explained.
As a whole, Johnson concluded this interactive tool will allow “not-so-awesome” techs to become better, and allow a shop’s highly skilled technician to reach even greater heights of efficiency.
Time Management
Mitchell also provided a way to get technicians in general to better use their time on the job.
When Johnson was a technician, he would punch a clock to track his time at work. That method merely showed that Johnson was physically in the shop, not necessarily how productive he was. The amount of repairs he completed would track that, along with how much he would be paid.
He would get an unpleasant surprise some paydays, when he learned all that time chatting it up at the parts counter led to less billable hours.
“If I didn’t pull my weight, the shop was less productive than it could have been,” Johnson noted.
Many years later, understanding the relationship between technicians’ time in the shop and their productivity is still something maintenance supervisors struggle with. And Mitchell 1 has provided a solution with its digital punch clock accessible via a smart device.
The update is now available for Mitchell 1’s Manager SE Truck Series software and provides shop management new ways to measure technician productivity they can use to enact change.
Accessible through smart devices, the software automatically generates productivity statistics as technicians clock in and out of labor operations, and it also enables users to track and report employee shift hours in real time on mobile devices.
“Once they log in, they can do the same things I used to do with that old-time clock—they can clock in when they get there, they clock out when they leave for lunch,” he said. The sign-in feature is geofenced so a tech cannot clock in or out from home or somewhere else.
Unlike a rusty punch clock on the wall, this digital time management program lists all the repair orders that are assigned, provides progress reports on each, how much time they spent on the repair, and how much they will get paid. When a tech steps away from a repair, they would pause the job.
If a technician billed 40 minutes, but the job took an hour and 20 minutes to complete, the technician knows they need to improve.
Managers can also run reports to identify the most productive workers as well as training opportunities.
Johnson explained a manager can sit down with a technician and show them “where they are kicking butt” and areas they need to improve, such as with electrical repairs. To get these features, users just need to perform a software update on TruckSeries. According to Johnson, more than 8,000 users have already received the update.
About the Author
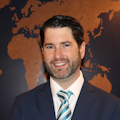
John Hitch
Editor-in-chief, Fleet Maintenance
John Hitch is the award-winning editor-in-chief of Fleet Maintenance, where his mission is to provide maintenance leaders and technicians with the the latest information on tools, strategies, and best practices to keep their fleets' commercial vehicles moving.
He is based out of Cleveland, Ohio, and has worked in the B2B journalism space for more than a decade. Hitch was previously senior editor for FleetOwner and before that was technology editor for IndustryWeek and and managing editor of New Equipment Digest.
Hitch graduated from Kent State University and was editor of the student magazine The Burr in 2009.
The former sonar technician served honorably aboard the fast-attack submarine USS Oklahoma City (SSN-723), where he participated in counter-drug ops, an under-ice expedition, and other missions he's not allowed to talk about for several more decades.