The design of the dispensing system needs to account for many factors. Joe Bamford, strategic account manager for SKF’s lubrication and fluid management brands, recommended evaluating the customer’s full range of system requirements to ensure a proper dispensing system design that meets their needs and to consider the following components and design factors:
- Fluid type: specifications/fluid viscosity
- Length of run: vertical rise/horizontal run/drop to reel bank
- Tubing or pipe to be used/ID size
- Elbows and T’s
- Filters/pulse meters/solenoid valves
- Dispense valves
- Reel: hose length/ID
- Flow rate (GPM): single or simultaneous dispense
- Tank room temperature
Taking all of this data into account, an approximate pressure drop figure can be generated. This data is then cross referenced with the manufacturer’s pump performance chart to best determine what pump offering (air motor size/ratio) will deliver the required performance.
“It is advisable to work with a certified engineer to evaluate the facilities and requirements, run calculations, create performance charts, and design a system based on real data,” Bamford said. “By taking an objective approach, it can be done correctly for new or existing facilities.”
Brian Morgan, national sales manager at JohnDow Industries, a manufacturer of oil and lubricant capture products, said shops should first pay attention to their equipment needs. “There are different ways of capturing lubricants from vehicles and emptying them into waste oil storage tanks,” he related. “And different types of lubricants need different solutions.”JohnDow offers low-profile oil drains to capture fluids from a vehicle, including 17- and 25-gallon steel oil drains that sit just ten inches above the ground and come equipped with a long reach T-handle and six-inch industrial casters for easy maneuvering and positioning beneath the unit. The company’s 25-gallon model for heavy-duty repair shops comes with a self-contained electric pump evacuation system with a 10' quick disconnect evacuation hose.
JohnDow also offers air-operated grease delivery systems that fit 35-, 120-, and 400-lb. grease containers and come with a 50:1 high-pressure pump, control handle, Z-swivel, drum cover, follower plate, and an 8' outlet hose. Additionally, the manufacturer provides aboveground used oil storage systems featuring a UL Listed double-wall tank that provides 110% secondary containment. The tanks are available in 180-, 245-, 285-, and 500-gallon capacities and have an air-operated 30 gpm diaphragm pump.
Graco Inc., a manufacturer of fluid handling equipment, recently introduced EGP electric transfer and on-demand pumps. Designed as replacements for the company’s obsolete APEX pumps, the EGP models offer optimized pump designs, new motors, built-in filtration, and new pressure controls for on-demand models. Available in 115VAC or 12VDC models, both EGP electric transfer and on-demand pumps are compatible with most standard electric configurations. By simply plugging the pump into a power source, an entire 55-gallon drum of 10W oil at room temperature can be emptied in less than eight minutes with the 8 gpm flow rate transfer model.
EGP pumps are also proven to be more energy efficient than pneumatic pumps, the manufacturer stated, offering an equally durable option for fleets and service providers seeking savings or who are unable to otherwise utilize compressed air.
Pump life in the EGP models is optimized with a built-in inlet strainer and motor over-temperature protection which prevent overheating, Graco added.
About the Author
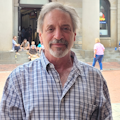
Seth Skydel
Seth Skydel, a veteran industry editor, has more than 36 years of experience in fleet management, trucking, and transportation and logistics publications. Today, in editorial and marketing roles, he writes about fleet, service, and transportation management, vehicle and information technology, and industry trends and issues.