The EV e-fluids revolution
While many know about the growing adoption of electric vehicles (EVs), few are aware that the lubrication technology for electric motors and other powertrain components is advancing at a similarly rapid pace. Called driveline e-fluids, these represent a significant technological advancement over traditional lubricants and will help fleets get the most out of their electrified investments.
Until recently, commercialized automatic transmission fluids (ATF) have been the lubricant of choice, but these are increasingly less suitable to meet the specific demands of the electric powertrain. Costly examples exist in fleet garages where a traditional gear oil had been used in error. These can corrode copper wiring, leading to motor burnouts and vehicle failure. Because of their cost, fleets need EVs operating as much as possible and failure is unacceptable.
Lubrizol’s research found replacing ATF with dedicated e-fluids formulated with the right additives can help alleviate these problems by protecting copper and electrical components while still providing gear protection. The key is to ensure that only the most suitable components are used in the fluid design phase.
It’s also worth noting that ATFs and e-fluids are not interchangeable. Though some ATF technology is marketed as appropriate for electric vehicles, the fact is that they were designed for traditional drivetrains. Improvements in aspects of fluid design such as supplements or “boosters” to existing additive packages are sometimes offered, but do not make them suited for the unique demands of an e-drivetrain.
E-fluids, by contrast, are developed as part of the transmission design process and are a technical component of the driveline—just like mechanical components. It’s evidence that OEMs are turning toward dedicated e-fluids for electric powertrains.
Advances in driveline e-fluids
Transmission fluids can be subject to extreme heat, especially when there is heavy current draw on the electrics in contact with the oil. E-fluids are therefore designed to be more stable to oxidation and thermal breakdown than many traditional fluids. Traditional fluids over time can also degrade to form corrosive sludge, adversely affecting the efficiency of component operation.
Where an unsuitable lubricating fluid is in contact with electrical equipment, there is always a risk of component corrosion, which is especially accelerated at high temperatures. In contrast, e-fluids have corrosion protection at their core with the inclusion of highly effective corrosion-inhibiting technology.
This offers demonstrable benefits for protection of copper connections, exposed motor wiring, and circuit boards. Corrosion can occur in copper components directly exposed to the oil but surprisingly also in unlubricated components above the oil because of corrosive vapors. A suitable e-fluid prevents this from occurring.
Specialized tests have been devised to screen for such corrosion protection. Lubrizol’s wire corrosion test uses bare wires and tests circuit boards to assess the protection abilities of the fluid.
The life of the e-motor and other electrical components is only as good as the life of the insulation, and thorough testing of the e-fluid ensures that resins and plastics are not damaged by it.
E-fluids generally have a lower viscosity than traditional fluids for a few reasons:
- A thinner fluid offers less resistance to moving parts, which improves the efficiency of the drive components and preserves battery range.
- Less-viscous oils are generally better at carrying away heat, which benefits the e-motor. A cooler e-motor is more efficient, and there is a beneficial effect on the lifetime of oil-cooled components because they have not had to run so hot for so long.
The thermal properties of an oil are more important than ever, and engineers must study the fluid’s thermal conductivity, heat capacity, fluid density, and viscosity profiles against temperature.
The electrical properties of lubricants are just as important in e-fluids as values such as viscosity, element content, and other performance characteristics. Three values typically measured for an e-fluid are:
- Electrical conductivity: how much electric current can be passed through an oil.
- Relative permittivity (or dielectric constant) related to the tendency of the oil not to store electrical charge.
- Dielectric breakdown strength, which is related to the ability of the oil itself to resist electric spark discharges.
Although the permittivity and dielectric breakdown values appear similar for many fluids, the electrical conductivity is highly dependent on the fluid viscosity and additives present. In general, most e-fluids are expected to be lower in electrical conductivity than traditional fluids, though it must be high enough to avoid electrostatic buildup.
The fluids are expected to protect steel gears, bearings, and other contacting surfaces from wear, which can be a challenge because specific additives can corrode the copper. To avoid this, judicious anti-wear chemical components are added to e-fluids. E-fluids are expected to provide suitable frictional performance to minimize noise, vibration, and harshness (NVH). The quieter-running feature expected of EVs is enhanced by stable friction modifiers, which eliminate NVH issues that can be caused by less suitable fluids.
Michael Gahagan is Technology Manager-Driveline for The Lubrizol Corporation in Wickliffe, Ohio.
About the Author
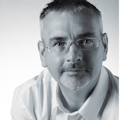
Michael Gahagan
Michael Gahagan is the Driveline Technology Manager for Lubrizol Corporation. He has worked for the company for 30 years.