Is manual or automatic greasing of truck components better?
There is no disputing the importance of ensuring all grease points on a commercial vehicle remain properly lubricated at all times. What’s up for debate, though, is how to actually go about applying the grease. Manual, auto, or something in between? One benefit of lubricating with a hand-operated grease gun is that the technician stays close to the vehicle.
“The ritual of greasing is an opportunity for inspection,” said Jay Boren, president of LockNLube, a manufacturer of grease guns, couplers, and greasing accessories. Using a manual grease gun also gives the technician a feel for how grease is moving into the fitting. Is the fitting taking grease easily, slowly, or not at all? Close proximity to that process helps determine if a fitting ever needs to be cleaned or replaced, for example.
Hand-greasing
As stated earlier, some fleets find hand-greasing does offer some benefits. Hand-greasing becomes even more appealing when the technician uses tools that make it easier.
The LockNLube Grease Coupler is one example. Bob Dietz & Sons, an excavation company in New Paltz, N.Y., has been using LockNLube couplers for years. Brian Dietz, co-owner, said they put them on every grease gun they have to lubricate their entire fleet of trucks and off-road equipment.
“Lubrication is just one of those things that’s a real hassle,” Dietz said. “Using LockNLube tips on our grease guns has totally transformed the process. Greasing is easier, faster, and cleaner. It’s also safer and more efficient because it becomes a one-handed process. You can even push grease into fittings that have been somewhat resistant.”
Read more: Lube it or lose it
Dietz & Sons uses a mix of lever-action and pistol-grip grease guns, as well as battery-operated tools. LockNLube’s Boren said a lever-action grease gun provides additional power over a pistol-grip. A lever-action also provides more grease per stroke, reducing the time and effort required to grease each fitting.
But the real key is the locking coupler.
“Without a good coupler, the technician is left wishing they had a third hand,” Boren said. The LockNLube is designed to create a leak-free connection while also ensuring that the coupler remains aligned with the entry point of the zerk and doesn’t pop off under pressure.
“To release a LockNLube coupler, the technician pushes down on the thumb lever and pulls straight back,” Boren explained. “Traditional couplers must be forced off to the side at a 15- or 20-degree angle, which can create issues with recessed fittings and other tight spaces.”
For these reasons, some fleets appreciate the hands-on approach to greasing. They also like the minimal upfront investment, as well as the fact that “weekly greasing” provides a sense of security. But there’s more to consider than simply the volume of grease being pumped into a fitting on a weekly basis. It’s how long that grease lasts.
This is where an automated solution may provide an additional level of protection.
Related content: The lowdown on grease
How an automated system works
To gain the efficiency benefits of an automated lubrication system, a fleet must spec the right-sized system for a given vehicle and application. But first let’s look at how an automated system is designed to function.
An automated greasing system is installed on the vehicle frame. Generally speaking, a pump distributes lubricant to different grease points through a series of hoses. Some sort of timer-based mechanism tells the pump when to send grease to a given grease point, along with how much.
Lubecore’s Multi-Line Spyder comes in three sizes, with reservoirs large enough to hold roughly four to 13 lbs. of grease.
“It’s important to match the grease reservoir capacity to the oil drain interval,” said Jan Eisses, president of Lubecore International, a manufacturer of automated lubrication systems. For instance, the larger size could allow 14 grease points to be properly greased for 100,000 miles. But maybe the fleet doesn’t need to go to 100,000 miles. It’s important to have this conversation with the lubrication system provider to choose the right option.
SKF has recently introduced an automated greasing system that is designed to make things even easier on the technician. “Anywhere you might normally use a grease gun is a good application for our new AECP (Automatic Electric Cartridge Pump),” said Jordan Butler, product line manager for North American automatic lubrication systems at SKF Group, a manufacturer of lubrication equipment, bearings, seals and other products.
The AECP draws its lubricant from a standard grease tube instead of a lubricant reservoir that needs to be occasionally refilled. That makes replenishing the system a little bit easier. According to Zach Cagle, strategic markets manager for mobile on-road at SKF Group, a tube of grease should last six to eight weeks under normal circumstances for a transport truck.
“We know certain grease points take certain amounts of grease,” Cagle said. “You set up the AECP system’s divider valve to deliver metered amounts of grease to the different fittings. It’s all timer-based. How often you tell it to turn on is based on application. In an medium-duty vehicle with a lot of stops and starts, you might program it to come on every three or four hours. A heavy-duty vehicle might be every couple of hours.”
Read more: Trends in automated manual transmission lubrication specifications
Benefits of automated greasing
“Some of these fleets will tell you that they get really good component wear when greasing by hand,” Eisses said. “It is true that frequency of lubrication is what gets you good component life. But those fleets doing it by hand every week are spending a lot of money on wasted grease, technician labor, and vehicle downtime. Also, every 3,000 miles (weekly) might not even be enough. You get component wear when a component goes dry, and that could happen at any time.”
With an automated lubrication system, the technician is removed from the greasing process, saving labor cost.
There is also the issue of downtime. On vehicles with longer drain intervals, Eisses said the only reason to bring a vehicle in for service on some occasions is to grease it. With an automated system, the greasing takes place while the vehicle is in operation. That allows the vehicle to stay in operation until its next oil drain.
When a vehicle finally does come in for its scheduled service, Eisses said most technicians will be more than happy to trade in their grease gun for a flashlight to simply perform a thorough vehicle inspection. Part of that inspection now includes the automated lubrication system.
“Check for evidence of fresh grease around all grease points,” Eisses advised. “Then you know the automated system’s pump is working and there aren’t any broken lines. It’s still a good idea to take a moment to inspect the lines for wear.”
Lubecore has developed a payback calculator to help fleets factor in all of the benefits of switching to an automated system. Eisses said an automated system can help a fleet save roughly $2,000 per year when compared to hand-greasing a truck driving 100,000 miles per year. The automated system is expected to pay for itself in two years, and savings are estimated at more than $16,000 over an eight-year vehicle lifecycle. Additionally, Eisses said a fleet should consider the likely extension of component life resulting from the more effective greasing an automated system provides.
Erb Transport Limited in Baden, Ontario, Canada, was an early adopter of automated lubrication systems more than 10 years ago. “Lubecore is our primary provider on all of our power units which includes long-haul sleeper tractors and regional tractors, as well as the Erb straight-truck fleet where lift gates are also protected by automated lubrication,” said Jim Pinder, senior corporate fleet director for Erb Transport.
According to Pinder, an automated system has allowed the Erb maintenance team to better schedule PM1 inspection timeframes knowing all components connected to the system are regularly lubricated. Additionally, due to the improved lubrication of the fifth wheel, steer tire and trailer tire wear have been reduced. “Trailer pin plates are also lasting longer since fifth-wheel grease is transferred to the trailer during operation,” Pinder explained. “Issues with seized brake components have also been eliminated, which extends brake lining life.”
Of course, a technician doesn’t have to worry about any of that if the vehicle has an automated lubrication system. However, the system has to work properly, and the fleet needs a plan for making sure it does.
“Because an automated system eliminates many of the machine’s regular walk-arounds, a leak or faulty line could go undetected and lead to components not receiving the lubrication they need,” Boren said. “When considering a switch to an automated system, be sure to include a plan for the operator to maintain daily inspections of the system and lines.”
Good preventive maintenance is all about keeping an eye on the vehicle. Whether hand-greasing or relying on an automated system, it’s important to keep those eyes wide open. The difference is in how the technician will be able to use their hands when that vehicle is in for service.
About the Author
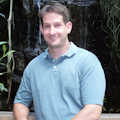