Fastener frustrations: A primer on removing broken bolts
Vehicle affected: All
Tools Used:
- Microtorch
- Screw extractor set
- Automatic center punch
- 3/8 drive ratchet and extension
- Various 3/8 drive 6-point sockets
- 3/8" reversible angle air drill
- Tap socket set
- WD-40 Rust Release
- Mitchell Pro Demand
- Protective equipment consisting of a heat sleeve, gloves and eyewear
- Non-flammable spray cleaner
- Compressed air (for cleaning around removed bolts)
- Thread chaser
Symptoms: Exhaust leaks at manifold caused by broken bolts
The first step in removing broken bolts is to try to avoid breaking them. In many cases a little preparation will allow you to remove a bolt that may be partially broken; or, in the case of fasteners used in exhaust or cooling systems, have a tendency to break upon removal. Understanding the fasteners can assist you in determining the best way to remove them.
Bolts used in cooling systems may have a rust build-up as well as damage to the bolt due to corrosion. Exhaust systems go through heat/cold cycles similar to heat-treating that can cause a bolt to shatter when you try to remove it. In this month’s Tool Briefing, we will guide you through some common steps that can be used to prevent a fastener from breaking as well as what to do if it does break.
Step 1: Preparing for the job
Let’s look at exhaust system retainers because they are undoubtedly the most common ones that break and more difficult to remove after they break. The use of dissimilar metals in engine manufacturing have necessitated a change in fastener technology, as well as in some cases, single-use bolts.
An aluminum cylinder head is going to grow and contract more and at a different rate than a cast iron exhaust manifold, so the bolts retaining the components as well as the method of installing them is different. Many vehicle manufacturers now use a thread-locking compound on exhaust manifold bolts. The thread locker acts as a lubricant during assembly and also keeps the bolt from loosening during the heat/cold (expansion and contraction) of the cylinder heads and exhaust manifolds during vehicle operation.
Exhaust bolts may be made of softer material than in the past so they are able to stretch during the heat/expansion cycles. In some instances, this will allow an easier extraction when they are removed, but in others the material will become harder and more difficult to remove because the bolt has been “heat-treated.”
As with any repair, check your information sources for TSBs and repair information for exhaust manifold removal paying particular attention to details such as torque specs, tightening sequences and manufacturer recommendations on bolt replacement as well as process information such as draining the cooling system or removal of additional components.
Step 2: Obtaining clear access
Always wear your personal protective equipment, consisting of a heat sleeve, gloves and eyewear. Begin by hoisting the vehicle on a service lift and remove all inner panels and skirts that will prevent you from having clear access to the manifold. If necessary, remove components such as power brake boosters or power steering pumps that may prevent you from having a straight pathway to the manifold bolts. Having access and free movement allowing the use of tools to be aligned on the same plane as the fastener is critical for removing bolts easily.
All technicians want to save time and have the tendency to remove as few components as we think we can get away with to speed up the job. In many cases, however, not removing a component can cause tools to be used on the wrong angle and put additional stress on a weak fastener. This can contribute to its breaking adding substantial time to the repair.
Step 3: Preparation for removal
Spray a liberal amount of WD-40 Rust Release or equivalent onto each bolt head and allow it to soak in for 10-15 minutes.
Then, use a ratchet and 6-point socket with the shortest extension that will allow you to turn each bolt on a straight angle and have free movement of the wrench. Loosen each bolt slightly. If you cannot move the bolt freely, try to tighten and loosen the bolt working it back and forth in order to break it free from corrosion. Loosening each bolt a little bit allows some tension to remain on the manifold and will decrease the pressure on any individual bolt, lessening the chance of it breaking.
Using a ratchet to break loose the bolts initially reduces the chance that a bolt will break from a “shock” as it might when an impact wrench or air ratchet is used. Once all of the bolts have been initially loosened, an air ratchet or impact wrench can be used.
Step 4: Removal of the broken fastener
The most critical aspects for easy bolt removal is to choose the correct extractor and that the hole for the extraction tool is centered. The correct extractor is determined by the circumstance.
If the bolt is broken flush with the head, a fluted spiral extractor, like tools in the Snap-On EXDL10 Extractor Set, works well in many instances, especially with its left-hand drill bits sometimes removing the bolt when drilling. However, this may cause the extractor to expand the bolt, making it tighter in the threads.
Using a straight fluted extractor, such as the Snap-On E10 from the E1020 Extractor Set, will work on many bolts by not expanding into them, but may not cut deep enough into the walls of the drilled bolt to grip it enough for removal. If the center of the hole is not exact, there is a chance that you could drill through the bolt into the head causing additional time and effort to repair the vehicle, or even drill into a coolant passage.
Using an automatic (spring-loaded) center punch, such as the Matco CP6, allows you to punch a small divot into the broken bolt and look to see if it is centered prior to drilling a hole. If it is not centered properly, move the center punch to the center and attempt to align it correctly, rechecking for center again. Using a larger center punch once you have found the center will enable you to make a large enough divot to ensure that a drill will not start “walking” when you drill a pilot hole.
Using the correct drill size and drill speed is necessary to make sure that you do not create additional work by having to remove a broken drill bit, typically a much harder task than removing a broken bolt. Using a left hand drill bit will also, in many cases, allow the drill bit to grip the bolt and spin it out. Select the correct extractor and drill bit listed for that extractor. A good rule of thumb is to use an extractor that is approximately half the size of the bolt, such as a 1/8 extractor for a 1/4" bolt, a 3/16 extractor for a 3/8" bolt, etc.
When you are drilling the pilot hole, it is necessary to make sure that you are drilling on the correct angle.
Installing a long bolt (6" or so) into one of the other exhaust manifold bolt holes will act as a guide for you to make sure you are holding the drill at the correct angle. Hold the drill on the same angle as the guide bolt and drill the bolt completely through the length being cautious to not drill into the cylinder head. In order to determine how deep to drill, use one of the other manifold bolts and note how much was threaded into the head. Using a drill stop or a mark on the drill bit will show when to stop drilling prior to reaching the cylinder head. Take care when drilling to set the speed of the drill to match the speed rating of the drill bit. Using a speed that is too fast will cause it to overheat and fail. Conversely, using a speed that is too slow can cause it to not cut properly. Use cutting oil to assist in lubricating and keeping the drill bit cool can prevent dulling the bit.
If bolts do break, heat can be your friend. If you have used any rust removal chemical on the bolts prior to attempting removal, you must clean that chemical off, since many of the chemicals are flammable and fire could be a concern. The Master Microtorch MT-51 is a great tool due to its size and the amount of heat it can generate. Using a full-sized torch is cumbersome as well as presenting a higher possibility of fire. Remember, any time you are using an open flame have a working fire extinguisher nearby and a co-worker spotting for fire.
Once the pilot hole is drilled, use the torch to heat up the cylinder head around the broken bolt keeping the heat away from the bolt as much as possible. Heating the cylinder head allows it to expand making it easier to remove the bolt as well as causing any thread locking compound to release for an easier removal. Heating the bolt will cause it to expand, tightening it on its threads.
Once you drill through the broken bolt, spray WD-40 into the hole. Insert the appropriate extractor and lightly tap it into place. Install the tap socket onto the extractor and slowly turn it to the left. Using a tap socket such as the Matco TS 705 allows use of a small ratchet on the extractor, in place of a T-handle, to provide more movement and keep the tool straight preventing side load which can break the extractor. Breaking the extractor, since it is an extremely hard tool and almost impossible to drill out, could necessitate removing the cylinder head and having a machine shop remove the broken tool. The fluted sides of the extractor will cut into the broken bolt allowing it to grip the bolt and twist it out.
Step 5: Completing the job
Once you have removed all of the broken bolts, use a non-flammable spray cleaner and compressed air to clean out the holes. Using a soft surface cleaning disc on the cylinder head and manifold, clean the mating surfaces. Using a hard surface disc can create scratches that will inhibit sealing.
Once that is done use the thread chaser to clean the threads and clean the holes again with the spray cleaner and air. Doing this assures that any rust or corrosion has been removed and also allows a clean surface for the thread locker or anti-seize product recommended by the vehicle manufacturer. Keep in mind you must use the correct product and assure it is safe for use on oxygen sensors.
It is a very good idea to replace all of the exhaust bolts or studs with new ones made of the material recommended by the manufacturer. If you use the wrong bolt or stud, you could create a situation where the bolt fails prematurely due to its inability to stretch at the proper rate matched to the components. Use a straight edge across the surface of the exhaust manifold surface to ensure it is flat and will mate to the head properly. Install a new manifold gasket without any sealer unless the manufacturer recommends it. Place the manifold and gasket on the head and install all of the bolts loosely. Starting all of the bolts assures that there are no alignment issues. Then, uUsing the information provided from Mitchell 1 ProDemand, tighten the bolts in the order and torque provided. Typically, bolts will be tightened by hand at the center then in order from the center out. Like most torque-to-yield bolts, you will need to tighten them to progressive torque specs until you reach the final specification. Since these bolts are requiring specific torques it is not recommended using air tools during the installation process.
Reinstall any components removed for access but do not install inner fender panels at this time. Start the vehicle, check for leaks, and fill and bleed the cooling system if it was drained. If the vehicle manufacturer recommends doing so, start the vehicle and re-torque the fasteners.
At this time you can reinstall any additional panels that were removed for access.
Taking the extra time and using the right tools to do this job properly is like any other, an investment in the repair that pays off by doing the job correctly and eliminating factors that can cause premature failures.
About the Author
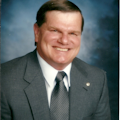
Barry Hoyland
Barry Hoyland has been in the independent aftermarket for more than 45 years as a technician, technician instructor, shop owner and shop management consultant. He owned and operated a successful Southern California automotive repair center that offers complete auto care and specialized in emission and diagnostic services for over 28 years. Hoyland also owned a company that modified vehicles to perform as emergency response units and mobile command centers, incorporating high-end electronic components into today’s vehicles. Barry has experience with all size and types of vehicles including traditional gas, hybrid electric, alternative fuel, and heavy duty diesel trucks.
Hoyland has provided consulting services for many automotive shops, fleets, and government agencies in order to improve their operational efficiencies.
In addition, Barry has worked with many NHRA drag racing teams as a crew chief on supercharged alcohol and nitro-methane fueled cars and currently serves as a crew chief on an Top Alcohol Funny Car, A Nostalgia Funny Car and a Nostalgia Alcohol Dragster
Hoyland holds certifications in ASE: A1, A6, A8 and L1, MACS 609, maintains a California Advanced Emission license, and a CDL with endorsements for double and triple trailers, tankers, and HazMat.
When he is not helping to run a shop in the Pacific Northwest, Hoyland travels across the U.S. as an instructor of technical and shop management courses, many of which he has developed.