Vehicle affected – All
Tools used:
· Brake Fluid Test Strips
· Vehicle Repair Information
· Bidirectional Scan Tool
· Brake Hydraulic System Flush Machine
· Brake Bleeder Screw Wrench
· Brake Line Wrench
· Venom Mini-Ductor
· Brake Fitting Rethreading Kit
· Mueller Kueps Brake Line Straightener
· Brake line bending tools
· Brake line flaring set
Brake hydraulic systems are relatively simple and maintenance-free, as long as you can keep moisture away from the inside and rust and corrosion away from the outside. If moisture enters the hydraulic fluid two things occur: a lower boiling point of the fluid, which can cause brake fade, and rust forming inside the system, which can affect the seals and pistons and bores of hydraulic components. One thing to keep in mind if you see signs of rust on hydraulic brake interior components (wheel or master cylinders, calipers, or brake lines) – there is a leak allowing air into the system. Just like an engine’s cooling system, rust cannot form unless air is entering into the closed system, so the presence of rust means there is air entering from somewhere. It can be from a caliper seal, a loose fitting, or possibly a faulty gasket on the master cylinder reservoir.
Exterior components that rust are typically not an issue unless you need to either service the system, such as bleeding the brakes, or replace a component where its removal is made more difficult from the rust. Even though I have spent most of my time in this business on the West Coast and have not had to deal with rust and corrosion from salt used to clear ice from roads, I have had to repair vehicles that had at some point been used in those areas, or deal with local vehicles that have been used or parked near the ocean, causing oxidation of undercar components. In this article, we will discuss some ways to overcome problems that rust or corrosion have caused in a brake system.
Issue: Moisture in the system
Step 1 – Determine if moisture exists in the hydraulic system
Since moisture is the start of rust, determining whether moisture is present is one of the first steps. One of the easiest and least expensive tools to use to test for contamination is a fluid test strip. Innovations over the past few years have allowed electronic testers to be available and less expensive, while also able to accurately test for contamination in any type of brake fluid with a single tool.
Step 2 – Remove the contaminated fluid
If moisture is detected, you must completely “flush” the system of the contaminated fluid. In my opinion, “flushing” the brake system on a late model vehicle with ABS is extremely difficult due to the complexity of the ABS module and the volume of brake fluid in the system. Most shops use brake fluid “flush machines” that are, in fact, fluid exchangers that do not completely replace all the fluid in the system.
Now, to flush a system, it is technically necessary to not only replace all of the fluid in the system but also use a flushing agent to clean the system, while simultaneously activating ABS solenoids to flush those components as well. Since most technicians do not have the equipment, nor the time, to completely flush the system, they exchange the majority of the fluid and assume the problem is taken care of. To help resolve possible residual contamination after a fluid exchange, drive the vehicle and safely activate the ABS system a few times, then re-test the fluid after the vehicle has been driven for a while to see if any moisture returns to the reservoir.
When performing a fluid exchange, it is a good idea to also bleed the brakes and even take a few extra minutes to collapse the calipers with the bleeder screw open in order to remove contaminated fluid at each caliper. Start by accessing your repair information database to determine what tools are required, and what the brake bleeding procedure is. Don’t forget to determine what the proper order of bleeding is, whether it is the traditional farthest from the master cylinder to the closest, or a variation of that due to ABS.
Next, you will need to see if a scan tool is required to activate the ABS system in order to allow the flow of fluid through the solenoids. If so, your scan tool will be used in the manner directed by both the vehicle information and by the scan tool user instructions.
Issue: Rust/corrosion on external brake components
Rust or corrosion on external brake components can include brake bleeder screws that are corroded so much that a wrench will not turn them, or so corroded that they break in an attempt to loosen them. One of the best ways I have found to deal with these is to spend a few moments prior to loosening or removing the component to clean and lube the part. I have had relatively good success by using WD-40 Specialist Rust Release and a wire brush to clean bleeder screws before removing them. I also use a bleeder screw wrench, which is a 6-point wrench, rather than a 12-point combination wrench, which not only can provide a better grip on the screw, but usually a better angle to work with.
For more stubborn parts, I use the Venom Mini-Ductor to heat the caliper or wheel cylinder housing to break the screw loose. This tool works very well for breaking loose brake lines as well.
Occasionally, a bleeder screw will be rounded off making it very difficult to remove with a wrench. In those cases, I will use the Bolt Biter from GEARWRENCH. This set of sockets will remove almost any bolt that has a stripped head by gripping it securely in its tapered grooves. Once the bleeder screw is removed, make sure the threads of the caliper or cylinder are clean and undamaged before installing a new bleeder screw.
If the threads are damaged, the LT993 brake rethreading kit by Lock Technologies (LTI), is a great tool to repair or clean threads while not damaging the seat of the female flared-end fitting. Using a typical tap will usually cause damage to the seat.
Replacing corroded brake lines can also be challenging. Not only will you need to remove a rounded off fitting, you will need to remove any fasteners or clamps that hold the brake line to the chassis, which are also typically rusted. The same type of tools you used on a rounded off or stubborn bleeder screw can be used to remove brake line fittings or hold down clamps.
When it comes to replacing a damaged brake line, you may be able to obtain an exact replacement from either the vehicle manufacturer or an aftermarket source. In many cases, you will need to bend your own replacement line to fit. In this case, you can either buy a straight line of the correct length or use multiple lines and a connector fitting if the length is too long for a single line. I do not like to add connector fittings, so I will use bulk line, typically made of stainless steel, to help avoid corrosion problems in the future.
The problem with using bulk line, especially stainless steel, is that the line typically comes coiled in a roll and is difficult to straighten prior to bending to shape. Mueller Kueps has made a tool for straightening either bulk line or re-straightening a bent line if it has been bent incorrectly. This tool slips over the line and allows you to straighten even the hardest stainless-steel tubing with ease.
When it comes to bending lines, it may be helpful to have a variety of benders. Since some brake lines have multiple compound bends, sometimes close together, a single design of a tool may not be enough. I use a combination of the OTC 6515 three-way bending tool and the Lisle 44150 pliers. This combination allows me to make sweeping bends with the OTC tool and close, tight bends with the pliers. The last step in making brake lines is flaring the end fitting. First of all, don’t forget to place the fitting on the tubing prior to flaring the end! A little hint here; if the last bend is close to where the end of the line and fitting will be, wait to make this bend until after the flare is made. Once the fitting is in place, use a high-quality double flaring tool to make the flare. Check carefully for cracks in the seating area once the flare is complete.
To summarize, having the correct tools to determine if contamination is present on internal components and the right tools to make repairs on external parts, can make brake service both easier and more profitable.
Tools Related to This Repair:
Mastercool Universal Hydraulic Flaring Tool Set https://www.vehicleservicepros.com/in-the-bay/tools-equipment/hand-tools/tube-bending-cutting-and-flaring-tools/product/21110342/mastercool-inc-universal-hydraulic-flaring-tool-set-no-72485
Lang Tools Brake Line Wrench
https://www.vehicleservicepros.com/vehicles/under-vehicle-trailer-towing/brakes/brake-lines/product/21108879/lang-tools-brake-line-wrench-set-no-5455
Cal-Van Mirror Tube Bender
https://www.vehicleservicepros.com/in-the-bay/tools-equipment/hand-tools/tube-bending-cutting-and-flaring-tools/product/21008936/calvan-tools-mirror-tube-bender-no-75902
Phoenix BrakeStrip Plus https://www.vehicleservicepros.com/in-the-bay/maintenance-service/chemicals/product/21030878/phoenix-systems-brakestrip-plus
About the Author
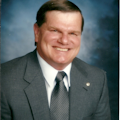
Barry Hoyland
Barry Hoyland has been in the independent aftermarket for more than 45 years as a technician, technician instructor, shop owner and shop management consultant. He owned and operated a successful Southern California automotive repair center that offers complete auto care and specialized in emission and diagnostic services for over 28 years. Hoyland also owned a company that modified vehicles to perform as emergency response units and mobile command centers, incorporating high-end electronic components into today’s vehicles. Barry has experience with all size and types of vehicles including traditional gas, hybrid electric, alternative fuel, and heavy duty diesel trucks.
Hoyland has provided consulting services for many automotive shops, fleets, and government agencies in order to improve their operational efficiencies.
In addition, Barry has worked with many NHRA drag racing teams as a crew chief on supercharged alcohol and nitro-methane fueled cars and currently serves as a crew chief on an Top Alcohol Funny Car, A Nostalgia Funny Car and a Nostalgia Alcohol Dragster
Hoyland holds certifications in ASE: A1, A6, A8 and L1, MACS 609, maintains a California Advanced Emission license, and a CDL with endorsements for double and triple trailers, tankers, and HazMat.
When he is not helping to run a shop in the Pacific Northwest, Hoyland travels across the U.S. as an instructor of technical and shop management courses, many of which he has developed.