How continuous improvement tools improve shop efficiency, uptime
With truck downtime becoming an increasing pain point for the industry, exacerbated by fewer technicians and parts immediately available, fleets are looking for two primary things in a maintenance partner: consistent quality and as soon as possible. And that is precisely what Gordon Truck Centers said it offers its Western U.S. customers.
“Our mission is to minimize vehicle downtime by providing consistently superior customer service across our network,” stated Pat Gendreau, COO at Gordon Truck Centers, Inc. “In our service operations we strive to ensure that repairs are completed within 24 hours by applying continuous improvement methods that streamline processes.”
Headquartered in Pacific, Washington, Gordon Truck Centers operates Freightliner, Western Star, Fuso and Wilson Trailer dealerships at 14 locations across Washington, Oregon, Idaho, and Hawaii. Included are Freightliner Northwest, Western Star Northwest and Freightliner of Hawaii. The company also has three body shops.
Across the Gordon Truck Centers network of dealerships there are 213 service bays. The facilities also offer mobile repair and preventive maintenance services. “Freightliner and Western Star make up the vast majority of our business,” Gendreau related, “although our 221 factory-trained and certified diesel and body shop technicians and hundreds of experienced parts and service staff also regularly work on medium- and heavy-duty commercial trucks of all types and makes.”
The company’s service processes begin with Express WriteUp from Daimler Trucks North America (DTNA). The tablet-based application allows managers to check in vehicles and create estimates and work orders. The mobile technology incorporates diagnostics, recalls and campaigns, and facilitates inspection processes.
Another diagnostic technology in use at Gordon Truck Centers shops is AmpNet for diagnosing battery and electrical system issues. The tool takes technicians through a step-by-step process for diagnosing issues with batteries, starters and alternators.
Gendreau also pointed out that at Gordon Truck Centers, Detroit Connect Virtual Technician remote diagnostics serves as a shared resource between fleets and dealership service staff. “When a truck has an issue, Virtual Technician sends an email to the fleet and the dealer with the fault code and the most common failure, and the nearest location with the necessary parts in stock,” he explained. “That streamlines repairs by giving us the ability to prepare in advance.”
Management of parts programs and technician recruiting are centralized and coordinated with service operations at Gordon Truck Centers dealerships. “We have a corporate department that works with our locations and we encourage local managers to work with vocational and high schools in their areas and provide employment opportunities for entry level technicians,” Gendreau related. “For newly hired technicians we have a mentorship program that includes onboarding related to our systems, policies and processes, and technical and on the job training.
“Through ongoing relationships with trade schools, some of our service managers are involved with curriculum advisory boards,” Gendreau added. “There is also a human resources person who has primary responsibility for maintaining our school relationships and who works in conjunction with our local managers. In addition, we have provided training aids, such as engines, and access to factory training content through a program developed by DTNA.”
Gendreau also credited DTNA for its support of the dealership’s service programs. “Elite Support provides direction on how to use lean principles to improve throughput, along with ongoing training and other resources,” he said. “The continuous improvement effort is focused on both service and parts. There’s also regular reporting and communication, including webinars on a wide variety of topics, along with a system for sharing best practices within the manufacturer’s entire dealer network.”
To validate all of its programs and practices, Gordon Truck Centers uses several measures. DTNA Elite Support criteria covers facilities, training, and customer expectations, while American Truck Dealers (ATD) and DTNA Dealer Benchmarking are used for tracking financial performance. In addition, key process indicators (KPIs) generated internally from a business intelligence system track shop throughput, technician efficiency, expenses, revenue, and gross profit.
“Each of our dealership locations has a continuous improvement team and Gordon Truck Centers has a corporate continuous improvement coordinator,” Gendreau said. “Every day, across all of our facilities, we strive to meet our goal of keeping customers on the road by actively identifying areas where we can improve the delivery of service. That approach is critical to our ongoing success.”
About the Author
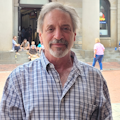
Seth Skydel
Seth Skydel, a veteran industry editor, has more than 36 years of experience in fleet management, trucking, and transportation and logistics publications. Today, in editorial and marketing roles, he writes about fleet, service, and transportation management, vehicle and information technology, and industry trends and issues.