Finding viable and cost-effective service solutions for the many repair challenges fleets face isn’t always easy. But they can be found as long as you work the problem before diving into a new or unique repair need.
“It’s the nature of our business that we often find ourselves looking at issues and repairs that can be out of our wheelhouse,” said Troy Willich, CEO and a co-founder of Fort Worth, Texas-based TDI Fleet Services. “Our sales team often brings us accounts that are in need of service and repairs on unique vehicles—equipment that dealers and other shops don’t want to work on because of their complexity.”
For example, how does a shop handle vehicles that work with chemicals? According to Willich, TDI has taken on trucks that haul rock-melting acid to oil fields, as well as paint-covered equipment that apply pavement markings on highways.
The maintainer also has had to deal with one fleet’s delivery trucks that used obsolete electric drive and battery systems.
“Our approach every time is to learn as much as we can,” Willich said. “At times, we reach out to partners to outsource repair work, as well as to the customer for help, before we try to tackle these types of challenges.
“We also research information available from manufacturers, although we’ve found getting help from dealers can be very challenging,” Willich continued. “There are also online forums where others have worked through similar problems and even YouTube videos have helped with troubleshooting and repair procedures.”
Willich related two recent repair challenges that came into the company’s 11-bay shop where that approach has worked.
Working on a customer’s tractor that had a significant oil leak behind the front engine cover, technicians in the TDI shop removed the overhead cams, replaced the seal, and began using the manufacturer’s online resources to follow procedures for reinstalling the gear sets, setting the spacing between the gears so they mesh correctly and timing the engine. While the oil leak was repaired, the engine exhibited a loud whine from the gears.
“We often outsource engine overhauls to a local partner, so we called them and they knew what the problem was immediately,” Willich related. “They told us that manufacturer’s procedures only work when you’re installing new gear sets, not when you’re reinstalling the components. After they told us what to do with the original gears, the truck was repaired quickly.”
Another example involved a trailer with a sliding suspension that had hit a curb and was out of alignment. The initial diagnosis revealed a slider box that was twisted out of shape.
“Once we removed the damaged component we realized it was fairly new and that it was assembled with HuckBolts rather than being welded,” Willich related. “After our shop manager reached out to the manufacturer, we learned it was designed that way so the frame could be bent back into shape without breaking a weld. All we had to do was use hydraulic winches and jacks to pull it square and the job was done.”
On a weekly basis, it’s not unusual for TDI Fleet Services to come across a repair challenge that forces it to step out of its comfort zone. Many times, Willich noted, it’s simple problems that turn into the biggest challenges for the truck and trailer service business. As the industry continues to see major changes in equipment design, including special features and specifications, staying up to date on the latest products and technologies and having a staff of highly trained technicians is increasingly important, he added.
“We still run into repairs that we need to research despite having a staff with decades of experience,” Willich stated. “That’s when we need the management insight to seek valuable input from manufacturers, partner shops, and any other sources we can find. The cost of that education in taking the time to research a problem before we decide to tackle it is minor when you consider the value of meeting a repair challenge so the turnaround time is shorter and our customer is happy.”
About the Author
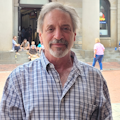
Seth Skydel
Seth Skydel, a veteran industry editor, has more than 36 years of experience in fleet management, trucking, and transportation and logistics publications. Today, in editorial and marketing roles, he writes about fleet, service, and transportation management, vehicle and information technology, and industry trends and issues.