Case for labor estimating tools to keep up with evolving technology
From a 30,000-foot view, all Class 8 trucks may seem alike, but upon closer inspection, each brand has its own unique characteristics. As FleetOwner editor-in-chief Josh Fisher pointed out in a recent column, it’s those differences that make each truck brand distinct.
The daily complexity with evolving technology
A skilled Class 8 technician can diagnose and fix most problems to get a truck back on the road. But consider the differences they encounter each day in each individual truck—what brand, what model, and what model year are they working on? Even within the same truck model, there can be variations by VIN that make one repair job different from another.
Add to that the rapid influx of new technology in the trucking industry, which is being adopted by more operators than ever before. The tech landscape today is vastly different compared to 20 years ago, and that adds another layer of expertise required by technicians to keep freight moving and ensure that repairs are completed efficiently.
As the number of different features on trucks grows exponentially, service facilities must deal with a multitude of different repairs through the variety of brands and models they see daily. OEM dealers may focus on a limited number of brands they service, while fleet service facilities handle a small range of nameplates and model years depending on their operation. The independent service facility can work on a wide variety of differently constructed vehicles as part of their business.
Labor time challenges across brands
Truck brands not only have distinctive systems, but determining labor time across different brands can be an added challenge for some service locations. A comprehensive labor estimating tool, such as the one included in Mitchell 1’s TruckSeries repair information, can help service providers accurately estimate labor-hour repair costs for each OEM and model.
An outsourced service provider must price work correctly, and labor is often the largest portion of the bill. Before the work even begins, customers require an accurate estimate. A reliable all-makes labor tool allows shops to deliver consistent, accurate repair estimates, improving both throughput and profitability.
Labor time to fix a type of repair on one truck won’t necessarily synchronize with the hours required for the same problem on another brand. Having that information is an advantage. Dealers often rely on OEM estimates for most of their work, but Mitchell 1’s labor estimating tool provides expected labor times for off-brand trucks or out-of-warranty repairs.
For fleets, this tool also offers a benchmarking target to measure technician efficiency and ensure they're quoted fair prices by external vendors.
Boosting technician performance
Whether it’s a dealer, an in-house fleet service, or an outsourced facility, labor tools help analyze technician performance and identify areas for improvement. With a clear understanding of how well a shop is performing, steps can be taken to boost productivity and profitability.
All Class 8 trucks may fit within certain industry parameters, but each brand is designed to satisfy the unique needs of its customers. Each truck brand has its own profile and personality, making the industry so fascinating. And it’s precisely why we should appreciate the technicians who keep those trucks running!
About the Author
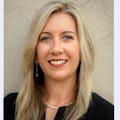
Kristy Coffman
Kristy Coffman serves as the Director of the Commercial Vehicle Group at Mitchell 1, the leading shop management and repair information systems provider in the automotive aftermarket. In her current role, she oversees all aspects of the commercial vehicle product line, including TruckSeries repair information software and Manager SE Truck Edition shop management system tailored for Class 4-8 trucks.
With a tenure dating back to 1997, Kristy initially joined Mitchell 1 as a customer service agent and has since navigated through various roles and responsibilities within the organization. Her journey has seen her take on pivotal positions such as product owner and manager, where she spearheaded software development initiatives and managed successful product launches.
In 2006, Kristy transitioned to associate product manager within the Commercial Vehicle Group, where her passion for the trucking industry flourished. Her core mission centers on developing and delivering products that empower technicians and shop owners to achieve success.
Kristy's professional background also includes significant roles at Maxwell Technologies, a global leader in energy storage and power delivery solutions for automotive and heavy transportation applications. Here, she served as a Fleet Sales Specialist and Senior Global Sales Planning Specialist, further expanding her expertise within the automotive technology sector.