To Marshall Sheldon, journeyman mobile technician at MHC Kenworth in Macon, Georgia, working the mobile maintenance beat is like running a small independent shop, and that’s one of the first lessons he instills in his apprentices.
“After they get a really good grasp on the fixing things, we focus on the business side of things, because every truck and every technician—to me—is its own little business.”
And while they break down the financial of running their truck, covering profit margins and expenses, the subjects of efficiency and waste inevitably come up when they get to the fuel line item.
“We need to manage our fuel consumption, so we need to idle our trucks as less as possible,” the MHC brand ambassador said. “We don't know what's going to go on in the economy; we need to run as lean as possible,”
A quick way to upskill new apprentices, Sheldon said, was by having them do each mobile truck inspections every Friday, so they pick up on where tools go and what’s onboard. When they run their own truck, all of that will be second nature and work will be done faster, he reasoned.
The mentor also makes the trainees who ride along with him write all the repair orders to build good habits.
“The more they do it, the more efficient they get at it,” he said. “My goal is always time to value, so when I get an apprentice, I want them to be profitable as quickly as possible.”
By following Sheldon, who has more than 15 years of maintenance experience, many in leadership roles, the new techs also pick up on the savvy vet’s tricks to make work more efficient. For example, he’s learned that sometimes the truck needing repairs is in softer dirt, so he has to park up to 100 yards away. Sheldon will carry whole socket trays, and various sized wrenches on a metal ring, to the work area so he does not have to waste time walking back and forth.
Another is rubbing oil or brake cleaner on metal tools versus washing them with soap and water to keep them from rusting.
He also sees the blunt truth as a solid way to reduce turnover and onboarding expenses.
“We don't have the time and the money to be worrying about replacing technicians when we could have just said, ‘Hey guys, we're cutting overtime—and this is why we're cutting overtime.”
He follows that up with telling them if they handle their business correctly, they’ll make it up with raises.
“If we're being efficient, we shouldn't have to work as many hours.”
In the mobile world, he argued overtime can be a safety hazard. “We don't want our people falling asleep at a wheel or working dangerously because they're tired.”
About the Author
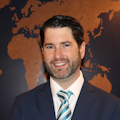
John Hitch
Editor-in-chief, Fleet Maintenance
John Hitch is the award-winning editor-in-chief of Fleet Maintenance, where his mission is to provide maintenance leaders and technicians with the the latest information on tools, strategies, and best practices to keep their fleets' commercial vehicles moving.
He is based out of Cleveland, Ohio, and has worked in the B2B journalism space for more than a decade. Hitch was previously senior editor for FleetOwner and before that was technology editor for IndustryWeek and and managing editor of New Equipment Digest.
Hitch graduated from Kent State University and was editor of the student magazine The Burr in 2009.
The former sonar technician served honorably aboard the fast-attack submarine USS Oklahoma City (SSN-723), where he participated in counter-drug ops, an under-ice expedition, and other missions he's not allowed to talk about for several more decades.