The introduction of telematics and mass sensorization on trucks over the past decade has enabled fleets to gather a lot of vehicle data. This information, in turn, has been used to power predictive maintenance (PdM). Historical fault code and repair data on particular makes and models are aggregated and fed into a data analytics platform. The algorithms inside crunch the data, look for failure patterns, and then make educated guesses on when a similar type of truck will need service to prevent failure.
For example, if the data shows three specific DTCs always appear two weeks before an issue causes an engine to derate, the fleet should anticipate that when those pop up together, the maintenance department should prioritize that unit and schedule repairs. They can refer to past repair history—maybe 90% of the time the NOX sensor went bad—to speed up the diagnostic and repair process, ultimately reducing downtime.
Condition-based maintenance, meanwhile, ditches the guessing game and focuses on the individual vehicle’s current health status. And it could become the preferred strategy for large fleets in the future.
Sandeep Kar, chief strategy officer at Noregon, noted there is a “rising demand for condition-based maintenance versus scheduled maintenance, and this is coming from the larger fleets.”
The executive had long opined that the industry needs to evolve from a rigid preventative strategy to a prescriptive model, where predictive insights are combined with root cause analysis to optimize maintenance schedules. But he also can see the benefits of focusing on the present.
He reasoned that while predictive strategies can inform on when alternators or brake pads typically should be swapped out, a platform that uses more real-time data provides the more suitable response for specific units. This is because factors such as geography and application matter.
Kar noted brake pad sensors allow a fleet to monitor system health more accurately than a fleet’s aggregate data, allowing them to optimize replacements based on that component’s condition. Ballparking parts replacement intervals based on educated guesses will inevitably lead to useful life and money being “left on the table,” Kar noted.
“When you have a fleet that has thousands of vehicles, we are talking about millions of dollars of savings if I can create a condition-based maintenance system versus a prescribed-schedule maintenance system,” he added.
But Kar noted full-scale adoption will require a “major cultural shift” in the industry and, more importantly, “top-notch solutions,” which he says aren’t quite there yet.
“They have to be highly accurate, otherwise it would actually be counterproductive,” he said.
Planning ahead
That means for now, fleets will settle for looking to the past to prevent failures in the future with PdM. The technology is progressively picking up steam as of late, though hasn’t had the major impact many have predicted. It’s been floated in the industry since at least March 2003, when the Technology & Maintenance Council had a technical session on “fleet prognostics.” At the latest TMC Annual Meeting, Fullbay reported that 12% of respondents in their 2025 State of Heavy-Duty Repair Report deployed PdM in the last year, though it was 29% for those performing in-house fleet repairs.
“What we see is everyone is asking about it, and no one knows what it means or what it’s going to do, or how they’re going to use it,” Fullbay CEO Patrick McKittrick explained.
That’s common with any newer technology, though maintenance departments should start to figure out how PdM could improve uptime.
At Geotab Connect 2025, Uptake CEO Adam McElhinney said predictive maintenance can increase fleet availability from less than 85% to 95%.
He noted predictive maintenance can change a fleet’s maintenance schedule from relying on OEM-recommended intervals and fleet experience based on miles or hours to “using more fine-grain data than just how many miles have elapsed since we last swapped out the coolant pump.”
“You’re essentially getting more vehicles for free for the cost of the vehicles you already have,” he said. He also posited that in terms of AI-based solutions’ impact on fleet management, PdM had an impact score around 7 or 8, second to autonomous driving’s perfect 10 score. Its viability score, the far more important factor for deployment now, was an 8 or 9, versus AI trucks’ viability of 2.
For those who do know how to leverage the technology, there’s still the issue of sifting through irrelevant data.
“Fleets are a little bit overloaded with work, and they’ve got to have better technology to help filter through the data and how to know what to focus on,” noted Brian Mulshine, senior director of maintenance products for Trimble.
“There are so many faults that people are not addressing today,” he continued. “On a truck, there are five computers and over 2,000 potential fault codes, but there are only about 120 fault codes that matter—ones that will shut down or derate the truck.”
McElhinney also noted that problem, with Geotab customers using Uptake reporting an additional 300 to 400 fault codes per Class 8 truck generated every month. He said it’s not uncommon for technicians to just clear the codes.
“A lot of time this results in you missing the true issues that are occurring on the vehicle,” the Uptake CEO said.
Uptake’s machine learning algorithms are trained to consider the sequence and duration of fault codes and ambient conditions on specific make and models and then offer recommendations. He likened it to how Netflix uses your viewing history to offer new titles to watch.
Mulshine noted engine manufacturers send customers spreadsheets listing fault codes they deem could cause issues down the road, and an API working through Trimble TMT is being developed to convert this data into action by generating work orders.
“Instead of sending an email to somebody that could be on vacation this week, why don’t we go ahead and just create the work order in their native system,” he reasoned.
Future is now?
FleetHD, a new entrant to the predictive space that recently emerged from stealth mode with its diagnostic maintenance platform, has been quietly working with some of America’s largest fleets to make CBM more feasible. The company, which works in tandem with various telematics and CMMS providers, integrates fault, sensor, DVIR data, and more into fleet maintenance management platforms like SAP, where its algorithm analyzes the data and converts that into actionable insights displayed on a dashboard.
They’ve also developed wireless brake pad sensors connected to the cloud via CAN bus, third-party telematics, or a mobile device to predict remaining useful life or when a truck may derate.
“We suck in all of the work order data, the real fix data, and all of the sensor information,” explained Steve Blair, co-founder and EVP of global sales at FleetHD. “We know the condition based on whether or not the brake pad or the tire is going to go down, and make decisions off of the data, historical information, and all the work orders for that fleet, then put it into our data lake and start training the model.”
That data, which FleetHD has gathered from large fleets for more than three years, might detect a combination of five signals or faults on a truck’s clutch that indicate imminent failure.
“Prescriptively, we know that a clutch is going to go out based on a combination of all of the data that we have,” Blair said. The system can then send recommendation notifications to the fleet to change it out.
The integrated info displayed on the dashboards also can show that when the truck comes in for that repair, upcoming regular PMs and defects noted on the DVIR can also be looked at, providing a full view of all of the actionable maintenance items, including parts required.
This has been valuable for FleetHD’s two Coca-Cola bottler fleets. “They’ve got close to 9,000 assets on the platform and we’re saving them millions of dollars just on driving better outcomes and mitigating unscheduled, unplanned downtime,” Blair said. He added FleetHD’s Coca-Cola customer also relayed that the solution maximizes uptime and has significantly reduced road calls and tows.
It also has direct benefits in the shop, with Blair saying the solution “increases mechanic productivity because we’re giving them precise fault-to-fix data. They’re quicker to fix trucks.”
Most importantly, moving toward a condition-based strategy should help fleets rely less on what history dictates and focus more on the present.
“When the sensor lets you know the brake’s remaining useful life is 15%, that’s real; that’s not some predictive algorithm,” he concluded.
About the Author
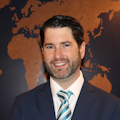
John Hitch
Editor-in-chief, Fleet Maintenance
John Hitch is the award-winning editor-in-chief of Fleet Maintenance, where his mission is to provide maintenance leaders and technicians with the the latest information on tools, strategies, and best practices to keep their fleets' commercial vehicles moving.
He is based out of Cleveland, Ohio, and has worked in the B2B journalism space for more than a decade. Hitch was previously senior editor for FleetOwner and before that was technology editor for IndustryWeek and and managing editor of New Equipment Digest.
Hitch graduated from Kent State University and was editor of the student magazine The Burr in 2009.
The former sonar technician served honorably aboard the fast-attack submarine USS Oklahoma City (SSN-723), where he participated in counter-drug ops, an under-ice expedition, and other missions he's not allowed to talk about for several more decades.