Meet Navistar’s International Truck 2023 Top Team technician
Navistar hosted its first Top Team technician skills competition in May of this year, offering ten technicians the chance to prove their skills, and one a sponsorship to TMC’s 2023 National Technician Skills Competition in September 2023 in Cleveland, Ohio.
Nathan Reed, a master-certified technician with RWC Group in Seattle, Washington, battled his way to the top out of the initial 420 technicians who tested to compete in Navistar’s 2023 Top Team skills competition. He then excelled among the top ten techs selected, demonstrating his mastery at 20 stations that covered everything from engines, air brakes, aftertreatment systems, electrical systems, wiring, and Diamond Logicelectrical system and fault codes.
“To be able to win this competition and come in first place is a huge honor for me,” said Reed. “At the end of the day, if the technicians aren’t there to get these trucks fixed, the whole thing stops. So, I’m proud of those who are here. There are some incredibly talented technicians who are here for this competition and I’m hoping that we can see that grow and recognize even more technicians as we go forward.”
Read more: Navistar launches technician skills competitionFleet Maintenance wanted to catch up with Navistar’s first Top Team champion after his win and discuss his day-to-day habits on the job, how his shop helped set him up for success, what the technician of 15 years loves most about his work.
Responses have been lightly edited for length and clarity.
Fleet Maintenance: How did you get involved in truck maintenance?
Nathan Reed: Through the Universal Technical Institute (UTI) in Avendale, AZ. I was always into cars when I was in middle and high school. I went to UTI for car knowledge and assumed I would end up at a car dealership. Since they offered medium- and heavy-duty diesel programs too, I took them because I really like learning and I wanted to expand my knowledge. Plus, diesel was becoming popular in the automotive industry. Once I started those classes, I thought the technology was cool and it shifted my whole focus. I was working at an independent automotive shop at the same time and switched to a diesel heavy-duty shop.
FM: What is your favorite part of job?
NR: Fixing the hardest stuff, the most complex problems that get me scratching my head. That is the most rewarding when you actually find the solution, especially when fixing the complicated trucks that other people could not find the solutions to.
FM: What was one of your biggest repair/diagnostic challenges and how did you solve it?
NR: I did have one a year ago that was having an intermittent communication issue. I had a second technician data link wiring and found the broken wire, just by watching when the engine control module was sending messages and when it wasn’t. Then I used wiggle testing to pinpoint the spot. That one took a lot of effort, 3 days in total. We had to figure out what modules were dropping off and when, and work backwards, getting a little bit of info each time the problem presented itself.
Otherwise, anything that is intermittent is challenging. When the problem is consistent and keeps happening, those are easy to solve, it is just a matter of tracking. Anything that is intermittent and comes and goes, that is the hardest because you have to catch it while it is doing it and gather the information to fix it. It takes more patience than anything else, wiggle testing, etc. Any time you get the opportunity to collect more data and narrow down the search toward your solution, that is the most difficult type of work.
FM: What are your favorite tools to use?
NR: My laptop, the EasyTech. I say that because we work on so much that is electronically controlled, so you use a laptop on almost every single repair. It is the most powerful and expensive tool that I own and has the ability to feed me a ton of information. As far as diagnostic work that I do most frequently, that is my go-to tool to see what the truck has to say for itself, and then use that information to figure out next steps.
FM: What do your supervisors and managers do to put you in a position to succeed?
NR: From a manager/supervisor perspective, their ability to help provide support to the technicians that we need is the biggest thing. They put us in a place to succeed by helping us get information from customers, write up repairs, and detect issues they are experiencing. We rely on service managers to get us specialty tools, like Navistar equipment, to fix these trucks. When you put that together, a manager that can bring all that support to us in one place helps us get troubleshooting done quickly and efficiently. It is a team effort throughout the entire coordination of the dealership.
FM: How does RWC Group show appreciation for your work? Ex. Bonuses, free lunches?
NR: We have a bonus program.
FM: What do you listen to at work?
NR: I work the night shift, so hard rock or heavy metal. We listen to a lot of comedy skits, too! We throw up people’s comedy routines on a speaker and it makes work fun. Night shift makes it easier to find a consensus on what we listen to as well.
FM: What do you like to do in your free time when you’re not turning wrenches?
NR: I do competitive rock crawling and love purpose-built cars (sand rail). I have a friend who drives and I work as his spotter. We do a west coast circuit for that; we have competed in a few states so far this year. I also do a lot of tinkering with 60s-80s Chevy and GMC pickup trucks, whether restoring, fixing, or tinkering around and learning about them. I really like those trucks for some reason.
About the Author
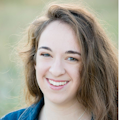
Alex Keenan
Alex Keenan is an Associate Editor for Fleet Maintenance magazine. She has written on a variety of topics for the past several years and recently joined the transportation industry, reviewing content covering technician challenges and breaking industry news. She holds a bachelor's degree in English from Colorado State University in Fort Collins, Colorado.