To keep good technicians, look at how fleets retain their best drivers
The trucking industry is at a critical juncture, with fleet maintenance professionals more essential than ever in keeping operations moving smoothly. Yet, the shortage of skilled technicians continues to strain shops nationwide, making it imperative for fleets to rethink recruitment, retention, and technology strategies to reduce turnover and build a resilient maintenance workforce.
A look into the labor shortage
Data shows us that the demand for qualified maintenance professionals is steadily rising, and a turning point for the industry. The Tech Force Foundation’s recent Supply & Demand report estimates that a total of 971,000 auto, diesel, collision and aviation technicians will be needed between 2024-2028, marking a 20% increase from the foundation’s previous projections.
When analyzing diesel technician employment rates, Tech Force’s report found that there are currently four times the number of replacement positions than new, underscoring the industry’s need to focus efforts on technician retention and advancement.
The increase in technician demand and turnover is putting real pressure on the fleet maintenance industry as it seeks new ways to attract and retain talent. Competitive wages and comprehensive training programs are essential, but fleets must also consider the investment in technology that simplifies complex diagnostics and streamlines shop workflows.
Fleets that embrace remote diagnostics and predictive maintenance tools today can enhance efficiency and reduce driver downtime, while at the same time increase workplace satisfaction for maintenance teams.
Learning from driver retention: Culture and compensation
Where does the current technician shortage we face come from? One can speculate, but it is likely a combination of deep-rooted challenges our industry has historically faced—including outdated perceptions of the profession, limited career visibility and insufficient mentorship opportunities.
Additionally, the general public’s lack of awareness of how the role of technicians has evolved may be part of it. As vehicles become increasingly sophisticated, maintenance jobs now demand advanced diagnostic skills, technical expertise and competence using digital tools—not just mechanical know-how.
Maintenance leaders can borrow successful strategies from driver retention programs by rethinking how they position the role to new employees. For example, fleets have found retention success by offering structured career paths, paid training and incentives tied to performance. This has helped shift the perception of driving from a short-term job to a long-term profession. Maintenance shops should do the same, focusing efforts on employee development and recognition.
Equally important is the work environment. Flexible scheduling, manageable workloads and a culture that respects technicians’ time are essential. Just as honoring home-time requests builds trust with drivers, respecting techs' time on and off the clock fosters loyalty, reduces burnout, and makes the shop a place where skilled professionals want to work.
New tech empowering drivers & maintenance pros
The last thing anyone in the transportation industry wants is for drivers and their vehicles to be stuck on the side of the road, especially in situations that could pose danger to the driver. These situations are especially frustrating when a maintenance issue could have been prevented.
A Federal Motor Carrier Safety Administration (FMCSA) study found that vehicle failure was a key factor in about 10% of truck crashes, with poor maintenance of brakes and tires being major contributors. These factors and more can be mitigated with the right preventative maintenance program.
Modern trucks are more technologically advanced than ever, equipped with sophisticated telematics, electronic control systems and alternative powertrains such as electric and hydrogen fuel cells. These innovations require maintenance teams to evolve from traditional hands-on repair technicians into skilled diagnosticians proficient in data analysis and new repair techniques.
The introduction of tools like Trimble’s revamped TMT Advanced Road Call module highlights the industry’s push toward cloud-based, data-driven maintenance solutions that improve uptime and operational efficiency. Today’s telematics platforms deliver much more than simple GPS tracking and now include predictive analytics, maintenance alerts and compliance monitoring that empower technicians to anticipate and address issues more proactively.
Investing in these technologies not only optimizes maintenance workflows but also supports technicians by reducing guesswork and enabling smarter decision-making, helping them work more effectively and avoid unnecessary stress in an increasingly complex environment.
With these new technologies in place, fleet drivers and maintenance professionals can work closer together to keep trucks moving on the road.
Building a workforce that thrives
While competitive pay remains a cornerstone of retention strategies, maintenance providers must look beyond wages to improve job satisfaction. Environmental factors within the shop can influence retention more than many realize. Newer service shops have incorporated features such as heated floors during winter months while efficient air conditioning in summer can create a more comfortable workspace that supports employee wellbeing.
Positive company culture plays a vital role as well. Maintenance teams who feel respected and valued are more likely to stay engaged and committed. Fleets that prioritize transparent communication, celebrate team successes, and invest in career development opportunities cultivate loyalty that pays dividends long-term.
The challenges facing fleet maintenance in 2025 are significant, but not insurmountable. By addressing the technician shortage through competitive compensation, enhanced workplace culture, and ongoing skills development, fleets can build a more stable and capable workforce. Coupling these efforts with investments in advanced diagnostics and predictive maintenance technologies will help shops increase efficiency and reduce costly downtime.
Fleet maintenance professionals are the backbone of trucking operations. Supporting them with the right tools, work environment and career opportunities are essential to keeping America’s supply chains moving forward.
About the Author
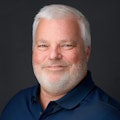
Brian Mulshine
Senior director of product management
Brian Mulshine is the senior director of product management for Trimble’s TMT solution and Connected Maintenance teams, where he is working to transform how the transportation industry performs maintenance while developing a seamless maintenance ecosystem for fleets of all sizes.
Mulshine has been part of the trucking industry for more than 30 years, most recently serving as the director of digital service delivery at Navistar International, where he led several significant product launches, including the International 360 portal and OnCommand Connection, as well as overseeing the integration between Navistar and Trimble’s Connected Maintenance solution.
Prior to his time at Navistar, Mulshine spent just over four years with Rush Enterprises, the largest truck dealer organization in North America, operating over 130 locations with a leasing operation of 8,000+ vehicles. While in this role, he supported the development planning for RushCare Service Connect, a call center and web application connecting more than 1,000 fleets to the Rush Service Network.
Additionally, Mulshine has been very involved with the ATAs’ Technology & Maintenance Council (TMC) and several other fleets, truck and engine manufacturers on a new Vehicle Maintenance Reporting Standards (VMRS) coding strategy, which aims to streamline and standardize maintenance activities across the transportation industry.