Steering retention with well-maintained suspensions
According to the Professional Driver Agency (PDA) Top Ten Driver Issues List of 2021, mechanical breakdowns frustrate drivers more than anything else. This study’s sample size was made up of tens of thousands of drivers over several years, PDA said, so fleets should take heed that the cost of downtime isn’t just measured in lost miles or missed deliveries, but also in how long a driver will tolerate their truck’s shop time.
It’s important to note that drivers, who are in high demand, won’t put up with road time fraught with misery, where poorly maintained shocks cause them to feel every bump in their bones, or poorly lubed components cause the steering wheel to shake. Over time, those can lead to physical breakdowns, with drivers calling off to get treatment for a nagging musculoskeletal injury. Or they’ll simply resign.
Spec’ing the right equipment for the duty cycle, combined with a proper preventive maintenance strategy, solid pre-trip inspections, and good driver habits are the surest way to avoid breakdowns in general. You also want to keep the driver’s body from breaking down. Prioritizing the spec’ing and maintenance of the suspension and steering systems becomes an elegant solution to both.
“Front axle and suspension maintenance is critical to ensuring the vehicle is being kept in prime condition,” said Sam Marco, senior product manager for front axle at Meritor, which makes suspensions, axles, and associated parts such as kingpins. “And that ultimately will translate to less driver fatigue and a driver staying focused when they’re behind the wheel.”
To reduce that fatigue through the development of new products, Marco looks at reducing three factors: noise, vibration, and harshness (NVH).
“All of those factors strain other components on the vehicle and then ultimately translate to potential driver fatigue,” he explained.
To reduce that fatigue, and keep drivers more comfortable at their company, fleet managers and maintenance supervisors need to understand how the various factors fit together. Everyone looks at these issues with a different lens, so to help discern the best approach for your fleet or shop, we gathered points of view from a variety of stakeholders. There is no one-size-fits-all approach, but the following advice should help steer your strategy in the right direction.
The driver’s perspective
“It makes a big difference when you got the right suspension,” asserted Bernie Gray, an owner-operator for about 30 years, who recently moved over to a driver trainer at J.J. Keller & Associates, a transportation safety consulting firm.
“That made life so much easier,” he recalled.
Life on the road was still hard, going for weeks on end hauling freight. Even with the best maintenance and comfortable ride, the road catches up with a body.
“What I used to be able to accomplish when I was younger is way different than what I can accomplish today,” he noted.
After 3 million safe miles, Gray opted for the trainer gig, teaching box truck and step-van drivers, along with some heavy-duty truckers, safe driving and pre- and post-trip inspections. Gray asserted that if he were to take on more freight, he would opt for a more comfortable ride versus slightly higher pay.
“I would much rather lease onto a company that has good, maintained trailers with air ride suspension, rather than spring ride, especially as an owner-operator, because I don't want that trailer beating up on me,” Gray surmised.
He said a bouncy trailer will tug at the tractor, and compensating for that strains the driver’s body while also risking damage to freight and exacerbating wear and tear on the truck.
Air ride systems cost more, and there are additional maintenance considerations. Air ride suspensions require air lines from the compressor, along with a regulator valve. The air bags themselves are also vulnerable to tears and damage.
“If you and your drivers take care of your suspension, your money comes back two-fold,” Gray said of air ride systems. He said part of this is due to less overall maintenance on the tractor-trailer, adding that third-party logistics carriers will also have a wider pool of customers, because “most shipping companies want air ride suspension over the spring rides.”
Gray also noted drivers who leave a fleet with best-in-class ride and steering will soon realize how good they had it after 1,000 painstaking miles in their new fleet’s truck with a suspect suspension. Call it resigner’s remorse.
Shop perspective
“I have been everything from a lube technician to a director of maintenance, and truck drivability and comfort has always been an issue,” said Tim Lamoreaux, truck service manager at North American Trailer, in Inver Grove Heights, Minnesota. “The drivers are in the trucks for 10-plus hours a day and to fight a pull in the steering or deal with vibration is understandably frustrating and fatiguing. I have seen drivers leave because of a drivability issue.”
Lamoreaux also worked at Blaine Brothers’ TruckAline business, which as the name suggests, handles alignments and other axle and suspension service items. The services are also used in-house on Blaine Brothers’ fleet of light- and medium-duty trucks, as well as tow trucks.
They use a mix of preventive maintenance scheduling and driver feedback.
“Our vehicles are on our PM program/schedule to monitor for upcoming or unexpected issues, and our heavy tow trucks are aligned whenever the steer axle tires are replaced or if there is a concern reported from our drivers on their DVIR,” noted Blaine Brothers CEO Dean Dally.
Dally also advised to seek out regular alignments at a reputable alignment shop.
“A good alignment shop should identify potential issues that may arise based on current tire wear patterns and with a good thorough inspection before doing the alignment,” he said.
This goes a long way in maximizing steer tire life.
“If the truck was aligned each time the steer tires were replaced, at a minimum, a lot of drivability issues could be avoided,” Dally asserted.
Lamoreaux added that shops should not align a truck with worn steering or suspension parts.
“Kingpins, steering linkages, and suspension pivot points are always checked and anything with play is shown to the customer to let them know our recommendation and let them decide whether to proceed,” he said. “Excessive play will not be aligned, and customers will be advised on repairs needed.”
This help shops retain customers, too, as a driver who feels off-balance after a fresh alignment would likely not return.
“We get drivers coming in from all over the country, and some of our biggest complaints that you’ll hear from drivers is when the truck just shakes and is always pulling in one direction,” said Irvin Bowman, owner of Ohio-based maintenance provider Wayne Truck and Trailer.
Bowman said many technicians aren’t sure what to look for, but the fix can be quite simple. For example, one might think the steering box is the issue when the truck is pulling, and replacing that leads to more cost and downtime. “Fifty percent of the time, it's not the box when you start getting complaints that way,” Bowman said.
The root cause more likely is a dry fifth wheel, which impedes the trailer’s movement.
“That makes the whole truck kind of feel like it’s darting back and forth on the road,” Bowman said. “It is rather nerve-racking if you ever take one for a drive.” A faulty kingpin may also be a culprit.
Wayne’s technicians are taught to check the basic, more common causes of steering issues first. This includes ensuring the wheels are greased, checking that U-joints and axle components move freely, and verifying adequate oil flow and pressure, Bowman said.
He also pointed out ignoring power steering fluid maintenance could have a big impact, which would affect the steering box. Power steering fluid could “go from doing great to terrible in a short amount of time,” he warned. Routine visual checks with a dipstick would alleviate this. If the fluid is not clear, but more brownish and foamy, there is a problem.
“There are a lot of trucks out there that have never had a filter changed on the power steering fluid—you’ll see them 10 years old or more sometimes come in with the original,” Bowman chuckled.
But what happens to the system as a result is no laughing matter. A low-level condition, from a leak or lack of steering fluid change-out, combined with a poor filter will cause the pump to cavitate.
“The pump starts shedding some metal, and it doesn’t take too long for that to take the whole system down,” Bowman said. Contaminants entering through the valves could also dilute the fluid and cause the truck to wander, he added.
Steering OE Perspective
Manufacturers also have found steering maintenance isn’t always a top priority.
“It’s a pretty simple thing to keep up on from a fleet standpoint, but we see a lot of times that there are fleets that don’t maintain the steering system at all,” said Jonathon Gerke, product manager at Bendix Commercial Vehicle Systems. This is based off examining returned steering gears. Bendix, which supplies aftermarket parts, also owns RH Sheppard.
Exact intervals are in the owner’s manual, but Gerke said steering fluid should be changed annually or every 100,000 miles.
“As that fluid breaks down over time, it’s not giving the lubricity,” Gerke explained. “Also, a lot of high-pressure seals in the gear start to break down as well because the fluid has a lot of contaminants in it.”
A problem is that steering troubleshooting is more specialized, and some technicians opt to simply replace the box. Gerke noted this “is not the most economical way,” as the manufacturer can reject warranty claims if the box is not the issue. Training and implementing a power steering analyzer (a type of pressure and flow gauge) would verify if the steering gear box is bad.
As Meritor’s Marco stated, the goal is to prevent NVH, which can crop up due to misalignments or worn components.
To verify a misalignment, investigate the tire wear pattern, Marco said.
“Tires are your key indicators of a problem, specifically within the front axle or within the suspension,” he said. Feathering is a dead giveaway. The tire will exhibit single-edge wear with cupping, or flat patches in the center.
A proper driver pre-check should detect this. Visual inspection will also spot tie rod issues. A driver or technician can then feel for movement to confirm suspicions. Fleets should also investigate when the driver mentions shaking or vibrating at certain rpms or speeds, Marco advised.
Staying consistent on kingpin lubing, as well as aligning the suspension whenever the tires are changed, are two easy methods to circumvent future steering issues as well as extend tire life, he said.
Suspension OE side
On the suspension side, maintenance is less of a concern, though that doesn’t mean they should be ignored.
“The parts of the suspension that are moving or operating on a regular basis over time are going to wear out,” explained Don Hester, senior program manager at Hendrickson.
The air springs warrant extra attention, as they are always working, so be sure to check for damage or wear.
“Shrapnel off the road can shoot into your suspension and slice the side of the air spring,” Hester said. “Maybe it’ll start as a small leak, but you need to pay attention or you’ll have significant damage to the air spring.”
Bill Hicks, SAF-Holland product manager, advised to “periodically check for road gravel or other abrasive debris between the cell and the piston and the bead plates. Removing the debris will help to prevent air cell abrasion and premature failure.”
Rubber extruding out of the side of the suspension can indicate damaged pivot bushings. This is more likely for severe off-road trucks, but a seriously unbalanced tire can also cause this, Hester said.
To prevent premature bushing and/or bushing core failure, technicians should also ensure the pivot fastener provides sufficient clamp load through the bushing, explained Hicks. “Therefore, it is good practice to re-torque the pivot connections every time you do a routine brake job, or every 50,000 to 100,000 miles,” he said. “In severe-duty applications, where brake jobs are performed more frequently, it is important to check torque more often.”
For new trailers, Hicks said that in order to ensure correct assembly and prevent damage, torque ratings must be checked on all critical fasteners at about 5,000 miles.
“Using a calibrated torque wrench is the only way to ensure they are at the correct torque level,” David Cary, chief engineer at Hutchens Industries, recommended. “Too much torque could damage components or the fasteners. Too little torque can result in wear of the components and fasteners.”
It’s more difficult to identify shock absorber issues. Working shocks heat up during use, so Hester advised to drive around first.
“Get this trailer bouncing up and down a little bit, bring it back into the shop, and then check the temperature of that shock relative to other steel components,” Hester said. “If they're not warm, that probably means they're not doing anything.”
Hester said a technician can use a thermal imager, and a working shock will be 10 to 20 degrees Fahrenheit above ambient temperature.
Hicks advised to visually inspect shocks weekly. This also helps detect leaks.
On the mechanical side, Hicks said new trailers should get their alignment checked after 1,000 miles. Every six months, or 25,000 miles (whichever comes first), leaf springs should get a thorough visual check and maintenance, if needed.
A technician should also re-torque all fasteners at that time, Hicks advised. This includes axle connection U-bolts, center equalizer bolts, the torque arms (both fixed and adjustable), and the spring retainer hold down bolts.
Trailers also are more prone to corrosion, as they have little to deflect road salt splashing up.
Hicks noted SAF suspension systems are treated with a hot dip galvanized level protection called Black Armour, which “chemically bonds with metal to form a protective layer that is impervious to water and stands up against the harsh anti-icing agents used on roadways.”
Cary said corrosion is often a hot topic, though recent design innovations have alleviated the issue. “Proper placement of drain holes, better frame designs and better coatings have gone a long way to curb that issue,” he said. “If an area of corrosion appears to have affected the structural integrity of a part, the manufacture should be consulted.”
And while not every technician is an expert in dealing with the systems that are crucial to driver comfort and freight integrity, Cary said that treating suspension maintenance like any other PM will result in less downtime.
“If it is kept up, it will have a minimal impact on your bottom line,” Cary concluded. “If a problem goes unchecked, it can lead to much larger issues with a greater impact on the company’s bottom line.”
About the Author
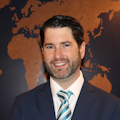
John Hitch
Editor-in-chief, Fleet Maintenance
John Hitch is the award-winning editor-in-chief of Fleet Maintenance, where his mission is to provide maintenance leaders and technicians with the the latest information on tools, strategies, and best practices to keep their fleets' commercial vehicles moving.
He is based out of Cleveland, Ohio, and has worked in the B2B journalism space for more than a decade. Hitch was previously senior editor for FleetOwner and before that was technology editor for IndustryWeek and and managing editor of New Equipment Digest.
Hitch graduated from Kent State University and was editor of the student magazine The Burr in 2009.
The former sonar technician served honorably aboard the fast-attack submarine USS Oklahoma City (SSN-723), where he participated in counter-drug ops, an under-ice expedition, and other missions he's not allowed to talk about for several more decades.