Corrosion prevention tips for electrical systems and wheel ends
Rust and corrosion will devastate a truck, rapidly aging metal until panels and parts practically disintegrate, or growing like an infection on electrical components. Left unaddressed, these kick off a domino effect of downtime and safety issues. And unfortunately, the sources are unavoidable and all around your trucks, from the ice-melting road chemicals below to the salty sea air all around.
You can't stop these factors, but you can focus the fight on two major areas: the electrical system and wheel ends. Here are some initial spec'ing tips and best maintenance practices to make sure these trouble spots don't crumble your assets' performance and lifespan.
Wiring & electrical systems
Electrical system connections, typically located in areas like the front of the trailer, the back of the cab, and near the tandem axles, are constantly exposed to road spray and deicing chemicals.
“Moisture also travels along the cables and into the connections, compounding the issue,” said Andy Summers, director of fleet sales at Phillips Industries.
When spec’ing electrical system connections, Summers said fleets should opt for:
- Over-molded plugs, sockets, and wiring harnesses to block moisture intrusion
- Sealed noseboxes and connectors (such as AMP-style connectors)
- Dielectric grease (a thin coating, applied on clean surfaces) to protect pins from moisture and corrosion
- Concentric jacketing that centers the copper strands in the insulation to reduce the risk of jacket breakage and moisture intrusion
Even though wire harnesses are tucked away, it’s still very difficult to keep them free from water and small debris, and harder to visually detect. They are also often routed over, under, or through metal crossmembers or other sharp surfaces. Together, these make a perfect breeding ground for corrosion.
“With vibration over time, the outer coating of a wiring harness can wear through, leaving exposed copper,” said Al Anderson, VP of sales and marketing at Peterson Mfg. “This is an open invitation for chemicals to enter the system.”
Anderson recommends choosing something with an IP69K rating, which validates a harness’s ability to effectively seal out moisture and debris. He also suggests working with the truck builder to make sure no terminal is exposed to the atmosphere, particularly the ground terminal.
“In some cases, like with our Peterson Defender harness, there are closed-loop systems where there are no chassis grounds,” Anderson said. “Everything runs clear back to the trailer nosebox, which eliminates any opportunity for corrosion to enter the system through the ground circuit.”
With lighting system components specifically, fleets should also look for properly sealed, weather-resistant products.
“The type of wire insulation also matters,” said John Hoover, VP of fleet at Truck-Lite. “Rubber insulation holds up better in high heat and UV exposure, while jacketed options that use GPT are ideal for heavy-duty use.”
For lighting itself, Hoover said to look for designs with potted circuit boards (where the electronics are sealed in epoxy) or conformal coatings, which help protect against moisture and contaminants. Also, make sure the lens and housing materials match the environment. Polycarbonate is great for impact resistance, while acrylic offers better protection against chemicals.
“It’s also smart to choose components with IP-rated connectors (like IP67 or IP68), which are tested to resist water and dust,” Hoover added. “Corrosion-resistant coatings on terminals and housings, such as anti-corrosive compounds, can also make a big difference in long-term durability.”
Smart spec’ing is a fleet’s first and most important step in the fight against corrosion. But sometimes corrosion will still happen. By remaining vigilant with inspections and using the right cleaning, prevention, and restoration products, fleets can take corrective action before it’s too late.
Corrosion risk factors
Fleets face a variety of factors that elevate the risk of corrosion even more, such as:
- Roadway deicing and anti-icing chemicals
- High humidity and wild temperature fluctuations
- Mountainous regions and stop-and-go urban routes under heavy load
- Hot and humid service shops
- Shops and storage yards close to the ocean (salt water)
Wheel ends
Wheel ends are constantly exposed to the elements, but that’s not the only reason they are high risk for rust.
“Wheel ends are also particularly vulnerable to corrosion due to brake pad dust,” said Scot Reeder, senior product manager at STEMCO. “The friction between brake pads and discs generates heat and releases iron particles. These particles can adhere to the wheel ends, promoting corrosion.”
When spec’ing wheel ends, material choice should play a major role.
“Most ferrous materials will need protection against corrosion,” said Jeff Larson, VP of engineering for core products at ConMet. “The type of protection will depend on their function and exposure. Alternatively, aluminum is mostly corrosion-resistant, which makes it a better material for guarding against rust in critical components like hubs.”
Another advantage of aluminum is that it doesn’t require any protective coatings like ferrous metals do. “Those protective measures help initially, but can wear off over time—especially under heavy use,” Larson said.
In addition to aluminum alloys, Reeder also said that stainless steel and composite materials, which optimize strength, weight, and corrosion resistance, can have their place when utilized correctly.
The protective coating is another thing fleets should look at, even when spec’ing aluminum, as different coatings provide additional unique benefits beyond just corrosion protection.
“Electroplating adds a protective layer to the metal surface,” Reeder continued. “However, it may not offer sufficient protection against prolonged exposure to corrosive environments. Powder coating provides a durable finish that resists chipping and scratching. Anodizing is particularly effective for aluminum, as it increases surface hardness. Ceramic coatings offer superior protection against wear.”
Troubleshooting yourself in the foot
One final piece of advice for protecting your electrical systems: Improper troubleshooting and repairs may inadvertently introduce corrosion to your system, which can spread into an army of faults.
“Poking a wire with a test probe leaves a hole in the wire for corrosive chemicals to enter,” Peterson’s Anderson said. “Always check for electrical current at the end of the harness, whether it be where the light is plugged into the harness or where one harness connection connects to another.”
Another repair tip Anderson offered is to avoid splicing a harness, if possible. It’s nearly impossible to make a splice completely waterproof, which can also allow chemicals into the system.
“If a repair is needed, find the closest place where the harness is plugged together and replace the damaged section,” Anderson advised. “Modular systems are more reliable and easier to repair correctly because you can just replace one section of a damaged electrical system.”
Unlike wiring harnesses, electrical system connections are often out in the open. Technicians should take advantage of that.
“Fleets should regularly inspect these components, especially from October to March in northern regions where road chemicals are used,” added Phillips Industries’ Summers.
Then, as a general rule, fleets should focus on back-of-cab connections, which are rarely unplugged and cleaned, but are the most vulnerable.
“During yard checks or whenever equipment is in for service, unplug the connectors, clean the pins and sockets with stainless steel or brass brushes, or use specialty tools like Phillips’ 4-123 kit for dual pole, and apply fresh dielectric grease,” Summers advised. “Don’t rely on annual PMs alone; incorporate this into regular maintenance. Also, keep replacement cartridges and sockets (e.g., QCP and 16-724 sockets) in [your]inventory, and treat worn pins and sockets as replaceable wear items.”
About the Author
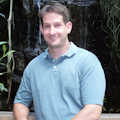
Gregg Wartgow
Gregg Wartgow is a freelancer who Fleet Maintenance has relied upon for many years, writing about virtually any trucking topic. He lives in Brodhead, Wisconsin.