How to properly execute a used engine oil analysis program
In a business environment where uptime and efficiency are at a premium, fleets should always strive to optimize their oil drain intervals (ODIs). A big part in knowing that perfect time to schedule an ODI is by performing a used-oil analysis. These can help a technician determine exactly when its time to bring in a vehicle for an oil change, and according to Paul Cigala, commercial vehicle lubricants applications engineer at ExxonMobil, regular sampling can help detect EGR cooler leaks, fuel dilution, and excessive wear metals inside of the engine, adding further to their preventative maintenance practices.
But understanding the benefits of a used-oil analysis is very different from understanding how to carry one out. Overall, used-oil analysis involves taking samples from oil while in the engine and testing for contaminants and lubricant chemical integrity.
“Optimally, you should have a sample of used oil analyzed after every oil change for every truck,” explained Karin Haumann, OEM technical services manager for Shell Lubricant Solutions.
This, she said, is the first step to getting to that target ODI. But you have to first know how to take that sample properly.
“If you take your sample when the oil is being drained, catch it midstream by waiting at least five seconds,” Haumann said. “That way, you won’t be collecting heavy metals or other deposits lying at the bottom of the pan.
“Withdrawing oil through the dip-stick opening is another good way to take the sample,” she added. “This can reduce the chance of outside dirt or contaminants getting into the sample and will keep the oil from splattering when you stick the bottle into the stream. Whichever way you take the sample, do it in the same manner each time to help keep your results consistent.”
Cigala also asserted where the oil is sampled from makes a big difference in getting accurate results.
“When you go to the doctor and they pull a blood sample, they’re not just making you bleed and then picking it up off of the floor,” he said. “They’re taking it out of a vein in a flow, and taking a representative sample of your blood and they’re looking at everything that they look at on the panel—it’s the same thing with used oil analysis.”
He said the sample should be taken from an engine that’s up to temperature, and either live under pressure out of the oil gallery or out of the middle of the oil pan through the dipstick tube.
ExxonMobil advises taking a sample via vacuum extraction with a vampire pump or from the in-line sample valve are both good options, though collecting oil from the sump drain after removing the drain plug is not. A few other best practices include keeping the oil sampling vacuum pump in a clean and controlled environment, as well as using new lengths of plastic suction tubing for each sample, which prevents cross-contamination. And always promptly send the sample to a lab.
Accurate reporting is crucial to help the lab do its jobs. The mileage on the engine determines if certain contaminants are normal or not. Until about 200,000 miles, engines will still have copper from when the manufacturer braised the oil coolers at the factory, and aluminum and potassium can come from the charge air cooler until an oxidative layer forms, Cigala said.
“What happens is as the hot air from the turbocharger goes across the charge air cooler, it picks up the aluminum and potassium, brings it into the combustion chamber, and then after combustion it finds its way into the engine oil,” he explained.
It’s also important to note that ODIs depend not only on the engine and engine oil, but the duty cycle.
“We always say ‘optimize,’ we never say extend your oil drain, because in a lot of cases, depending on where the fleets are operating and the drivers, there’s a lot of variability and [maintenance providers] need to really have a good picture of what’s happening there,” said Rebecca Zwetzig, Chevron, ISO clean project manager for the Americas.
She said three factors will ensure optimized oil: “Start clean, monitor that fluid health with a fluid analysis program, and then keep it clean.”
This year Chevron rolled out its Keep Clean Preferred Vendor Program to provide shops a network to find the right tools and partners, which ensures oil does not get contaminated before being poured into the engine and while in service through oil monitoring. Vendors include fluid management company Des Case and oil and fluid sampling provider Checkfluid.
“We don’t have tools or an offering in that category, and many times our sales representatives are getting asked questions about that,” Zwetzig said. “We felt there was a gap here that we could help fill for those who are seeking a solution in this area with quality vendors who provide top-notch service and have the expertise to deliver upon that.”
According to Jason Bendon, chief commercial officer of Des Case, “80% of failures on the mobile side are directly related to contamination.”
“You just have to have enough data to be able to measure it, which is why taking that sample is so critical,” Zwetzig concluded. “This leads to more uptime, higher equipment availability—and components that last longer means a significant reduction in expenditures to a fleet’s capex budget.”
About the Author
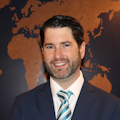
John Hitch
Editor-in-chief, Fleet Maintenance
John Hitch is the award-winning editor-in-chief of Fleet Maintenance, where his mission is to provide maintenance leaders and technicians with the the latest information on tools, strategies, and best practices to keep their fleets' commercial vehicles moving.
He is based out of Cleveland, Ohio, and has worked in the B2B journalism space for more than a decade. Hitch was previously senior editor for FleetOwner and before that was technology editor for IndustryWeek and and managing editor of New Equipment Digest.
Hitch graduated from Kent State University and was editor of the student magazine The Burr in 2009.
The former sonar technician served honorably aboard the fast-attack submarine USS Oklahoma City (SSN-723), where he participated in counter-drug ops, an under-ice expedition, and other missions he's not allowed to talk about for several more decades.