This is Part One of a two-part story.
Discussions around how artificial intelligence will revolutionize the trucking industry often turn to topics like load optimization, routing, driver safety, and vehicle autonomy. Predictive maintenance also ranks high on the list, since AI can analyze an insane amount of diagnostic and repair information. We go into greater detail on page 14 about that, but how can this advanced AI help shop managers work smarter, not harder?
“The big benefit of AI is that it reduces time to insight,” said Mike Branch, VP of data and analytics at Geotab, a telematics provider that has also developed an AI-powered fleet management platform that does just that.
Now a new form of the technology, generative AI, is at a fleet’s beck and call. It allows you to prompt the program with a question or request, and AI answers in text, image, or even video. Consumer versions may be used to provide a recipe, summarize “War and Peace” in Spanish, or create art. As generative AI evolves, it should be able to help a shop manager calculate budgets or track labor simply by asking.
“That doesn’t mean a maintenance or shop manager can completely do away with spreadsheets, reports, and dashboards,” Branch pointed out. “But when you have a specific bit of data you want, AI is like having a data scientist in your back pocket.”
To expand what these pocket assistants can do for fleets, last summer Geotab began beta testing a new AI-driven solution, referred to as Project G, with fleet customers. During the first stage of testing, the AI was only trained on a specific subset of data from Geotab’s Data Connector tool, including asset utilization, fuel economy, and idling.
But fleets were asking the AI a lot of questions that required data beyond what Data Connector could provide. Now Geotab has begun incorporating additional telematics data from the vehicle—such as remaining useful oil life, battery condition, and DPF condition—to help maintenance managers gain further insights and improve maintenance scheduling.
Read more: How to unleash the power of predictive maintenance
This is still like a souped-up predictive maintenance use case. The considerable IQ of available AI solutions can be used for so much more in the shop, really only limited by the users’ creativity and imagination. The problem for most managers, though, is finding time to step away to let their imaginations run wild. Fortunately, the AI that exists right now can perform several tedious tasks to help free your mind.
Technician support
Many jobs will be drastically changed, and some replaced, as AI becomes increasingly embedded in the workforce and is able to do more jobs. In the hands-on vehicle maintenance sector, AI can’t replace brakes or change oil, but it can serve as an extra helping hand in the shop. And asking for that help is getting easier.
“The big revolution we’re talking about is a shop manager having the ability to interact with an AI machine-learning model by simply typing out a sentence,” said Jacob Findlay, co-founder and executive chairman of Fullbay, a heavy-duty repair shop management platform. “And think about a technician having the ability to talk to an AI-powered software to have it create a work order, all while that technician is under a truck.”
With onboard components getting more intelligent, and the supply of human labor getting more scarce, this help should be a welcome addition.
“In an industry where there are more trucks on the road but fewer technicians to repair them, we need this type of technology,” Findlay noted.
The Fullbay founder tends to get a little excited when talking about the realm of possibilities AI brings to the table. The Fullbay platform’s current software functionality ranges from generating estimates and invoices to preventive maintenance tracking and parts inventory management. It also allows shops to generate various reports to help track things like technician efficiency and vehicle cost of ownership. When you think about all of that functionality, there are numerous tasks that could be automated by AI. Additionally, many tasks could be simplified by allowing a well-trained AI tool to retrieve and analyze data. And make no mistake—Fullbay is full of data.
“This puts us in a really good spot to leverage AI [at some point],” Findlay said. “With the vast amount of highly detailed work order and repair information data that’s entered into our system, we’re in a position to do specialized AI training that is proprietary.”
As a hypothetical example, Fullbay’s repair history data shows that it’s common for a technician to simply swap out a sensor when it’s giving them problems, but that doesn’t solve the root cause of the problem. Now let’s say a technician working in a shop 1,000 miles away does solve the root cause. With AI scanning and analyzing all the repair orders that have gone through the platform, the next technician to encounter this same sensor issue could ask the AI tool what some possible causes are. The AI could suggest what that disparate technician already figured out.
“No human being could ever consume all of that information,” Findlay pointed out. “So from that standpoint, AI could end up becoming the best diagnostic tech in a shop.”
Until that day comes, a shop manager can already take advantage of several “generic” AI tools to assist them in various aspects of their jobs, such as to quickly research certain information, analyze data, create charts and graphs, write emails, or automate scheduling.
Scheduling and parts inventory
“Maintenance professionals often rely on their mobile devices to perform day-to-day tasks and reporting,” said Evan Welbourne, head of AI and data at Samsara, provider of the Connected Operations Cloud platform that harnesses IoT (internet of things) data to develop actionable insights for fleets. “AI can be used to streamline and simplify these processes by automating particular tasks and surfacing curated workflows for specific employees, cutting out the noise and only providing them with the information they need for a given task, at a given time.”
Employee scheduling is another management function where AI tools already exist. A software company called Celayix uses AI machine learning to study past schedules and various rules the user has set up to automatically schedule shifts that meet certain requirements and operational needs.
Read more: Decisiv/TMC report: Parts, labor costs stabilized in Q4 2023
Parts management is another area where AI can play a beneficial role. Yes, there are already plenty of shop software platforms out there that possess the functionality to track inventory levels and even set reorder points. But AI can more deeply analyze historical usage data along with additional external factors in real-time (i.e., price, supply, and demand) to help determine what the optimum min/max and reorder levels should be at various points throughout the year.
Through image recognition and machine learning, AI can also help maintenance professionals look up parts faster. The user just takes a photo of the part, uploads it to the software, and AI searches for a match. At a point in time when the fleet maintenance industry is losing a lot of tribal knowledge due to an aging workforce, this type of technology will become essential.
In addition to the general types of AI tools just described, there are also some industry-specific examples of AI being put into action. This is an important development. The real potential of AI lies in industry-specific tools trained on specific data that a maintenance manager can feel comfortable in trusting.
Automatic VMRS encoding
The TMC’s Vehicle Maintenance Reporting Standard (VMRS) codes have been developed to keep dealers, repair shops, and fleets on the same page when a vehicle is being serviced. The challenge is that technicians often fail to assign a VMRS code when servicing a vehicle. That makes it harder for a fleet to understand what’s happening in the service bay so it can accurately measure things like M&R costs and TCO.
“We’ve begun using AI in the VMRS encoding of operations,” said Nick Pittinger, director of data services at Decisiv, whose Service Relationship Management (SRM) Ecosystem has more than 7 million assets in operation, along with 5,000 dealers and service providers, and more than 74,000 fleets and asset owners. Needless to say, the Decisiv SRM Ecosystem sees a tsunami of service orders, around 300,000 per month. All of that data is used to develop AI algorithms and machine learning to recognize certain information defined during a service operation, and then encode it with the appropriate VMRS code.
Currently, Decisiv’s AI is automating the encoding of the VMRS system-level code (Code Key 31). That enables people downstream of the repair to gain better maintenance insights, and even perform tasks like warranty claim submission. Pittinger said they’ve been seeing 80-85% accuracy on hundreds of thousands of repair operations per month. That’s a huge improvement considering how VMRS codes were only being provided on 5-10% of the repairs when a technician did it manually.
Given this initial success, Pittinger’s data team is looking into the automation of additional VMRS codes. A logical next step would be the assembly-level Code Key 32. From there, Decisiv’s fleet customers have been asking about things like Code Key 14 “reason for repair” and Code Key 15 “work accomplished.”
To read more about how AI can assist back-office processes, see Part Two of this story when it becomes available.
About the Author
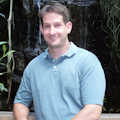
Gregg Wartgow
Gregg Wartgow is a freelancer who Fleet Maintenance has relied upon for many years, writing about virtually any trucking topic. He lives in Brodhead, Wisconsin.