Apprenticeships: The sustainable way to solve tech shortage
This is Part 2 of a Fleet Maintenance's 3-part series on hiring and retaining technicians in the commercial vehicle sector. Read Part 1 here.
The transportation industry needs technicians to maintain and repair all those rolling assets across the country, but many of the educational trees they used to grow off of were thrown in the wood chipper long ago. Lamenting that will do nothing for truck uptime, so fleets must now find new sources from which to harvest new quality technicians, because the old branches are gone.
“If you wait on the current system to produce, you will be waiting for a long, long time,” said Tim Spurlock, CEO and co-founder of American Diesel Training Centers. “The current system is irreparably broken.”
The candid maintenance advocate may lack faith in America’s trade education pipeline but believes a big share of entry-level work can be taught in-house.
“Most companies will tell you that their most important job is a PM (preventive maintenance)—brakes, electrical, diagnostics,” Spurlock said. “The only way to get this is to grow your own.”
There’s no one way to find technicians to grow, so you’ll likely want to try more than one. This goes beyond hanging “Help Wanted” signs and posting to online job sites such as Indeed, ZipRecruiter, or others.
Mega dealers have the capital to fly out to premier diesel schools and pitch pending graduates on what they can offer. These technicians were molded to provide immediate help, with a foundation to build even more skills. If one of these schools is not near you, diesel, or auto programs are offered via a community college or technical school. Job fairs, outreach to high school and vocational programs, and open houses can all get leads as well.
At the very least, transportation stakeholders in need of technically adept workers should have open lines of communication with the various high school and post-secondary schools. This may include joining an advisory board, making curriculum suggestions, or donating equipment.
And lack of time is no excuse, said Robert Braswell, executive director of American Trucking Associations’ Technology & Maintenance Council.
“It’s either important for you, or it’s not important for you,” he asserted. “If I don’t have time to brush my teeth this morning, well, there’s a consequence to pay for that—my teeth are going to fall out. Whether you’re a big fleet or a small fleet or a small shop, I think there is a certain amount of time that you can give to that sort of thing, even if you just reach out to the schools in your area and find out what their curriculum is.”
“While it takes time, it allows the business to choose and nurture the technicians who will grow with them and are more likely to stay long-term,” ASE President Mike Coley noted.
George Arrants, VP at ASE Education Foundation, said he believes reaching these students during their education will mitigate those early losses, which break down 20% of diesel students choosing another path right after graduating from a high school vocational or post-secondary trade program, and another 21% leaving within two years.
“Partnering with schools allows shops to directly mentor students during the education process and proactively address any issues they may have before they quit the trade,” he advised.
Spurlock is skeptical of this approach, questioning how a company would aggregate this approach: “There are no high school diesel programs in Columbus and five auto programs with a total enrollment of maybe 150 kids. I’ve spoken at most of them. Moreover, the majority of students in these programs are not ready for a real shop environment. You’re throwing an 18-year-old kid into a tough environment with 30- to 40-year-olds. It’s tough.”
Diesel Laptops’ Robertson also questioned how much effort should be placed in high schools.
“It’s kind of an unpopular opinion, but I don’t see how going into high schools is really going to move the needle on anything,” he admitted. “We’ve been talking about that for over a decade. The fact is, we look at every stat that ever exists. Most high school seniors already know what they want to do before somebody shows up and says you should do this profession.”
Robertson believes a better strategy is to “go find people in their early 20s, people who may have had a life that’s been a little rough, and who have a job that takes a lot of energy and is physical but doesn’t pay that well.” He said this includes manual laborers, servers, and line cooks. It could also be someone who isn’t as happy in another industry or a veteran. NVI has one of each in the September graduating class.
Pitt Ohio has found some success by working directly with vocational students, according to Taki Darakos, the midsized fleet’s VP of maintenance and fleet services. It has cooperative programs with vocational schools in Pittsburgh and Hermitage, Pennsylvania.
“It’s been wonderful—18-year-olds coming in, working in the shop part of the time and going to school the rest of the time,” Darakos explained.
He said these potential techs learn basic skills, how to work safely, and how to communicate and interact with teammates.
Those experienced techs also benefit from what Darakos calls the “co-op factor.”
“It’s also been great for our seasoned techs because there’s so much excitement when these young kids are showing energy and enthusiasm and wanting to grow and learn,” he said.
These seedlings won’t flourish in any and every shop environment, though. “It’s got to be the right shop and the right mentorship,” said Darakos, who has a biology degree and looks at these issues in a naturalistic way. “But you get those things right, and it’s like a symbiotic relationship.”
Darakos worries about the pending imbalance happening in the industry that could throw off the homeostasis.
“The one thing that keeps me up at night is that there are so many people leaving and retiring from the industry, and then you have an influx of young talent,” he said. This loss of solid mentors could disrupt the shop, and younger techs could become disengaged.
That’s why when you find technicians who want to work for you, the most important thing is to not let them go.
Attention on retention
Darakos advised that like older trucks and budding plants, young technicians need plenty of maintenance and care.
“If you’re not watering and fertilizing these techs with experiences, knowledge, and education, the newness—the excitement on the job—is eventually going to go away, and they’re going to leave you,” he warned.
The fleet executive also found that the first one to two years is pivotal. “That’s a really critical time where you’ve got to pay extra attention to people and make sure they have the support to continue,” Darakos said.
Supervisors should ensure new techs are “fitting into the shop, fitting into the culture of the organization, and feel valued and like they’re getting everything they were looking for,” he added.
Instilling a sense of value comes from trust, and that likely means giving technicians more responsibilities.
“The most important thing that companies can do is provide continuous training and a pathway to promotion,” Spurlock said. “If someone is ready, promote them. It doesn’t matter if they’ve been working for two months or two years. Treat techs like a valuable investment, not a commodity.”
Robertson agreed that the keys to retaining newer technicians are training and a solid career path.
“Because someone’s always going to offer more money, how do you keep them in there?” he asked. “You’ve got to keep them engaged and make it a great place to work.”
Braswell encourages fleets to provide newer technicians with “a clear career path where they can make improvements during those first two years.” Once they make those improvements, they need positive reinforcement, such as a raise, perk, or benefit, he explained.
“That is a tried-and-true method … and a lot of companies will simply ignore that,” Braswell lamented. “All they do is get a warm body in there, and they don’t give it any thought after that. And that’s a recipe for disaster and usually why you find a lot of these folks are leaving six months after they get hired.”
This is backed up by a late 2021 survey by Navistar’s dealer service development and market research teams, and the findings were paired with qualitative and quantitative research. The goal was to find what service departments need to improve retention; what motivates technicians and senior advisors; and what competitive compensation, benefits, and career opportunities look like, explained Ana Salcido, Navistar’s technician recruitment manager.
“The biggest finding? Compensation and benefits get technicians in the door, but management and culture are what retain and motivate talented employees,” Salcido noted.
To further motivate and recognize employees, the OEM introduced the Technician of Influence award, given to four high-performing employees per month “for going the extra mile and demonstrating responsibility, trust, proficiency, and productivity,” according to Salcido.
Master tech and apprentice
Braswell advised that maintenance management set up a functioning apprenticeship program to ensure those technicians that were so difficult to find stay at your company. TMC’s S.5 Fleet Maintenance Management Study Group and Educator Committee released the Model Registered Apprenticeship Program for Commercial Vehicle Technicians to offer a roadmap on how to set up an apprenticeship program and monitor apprenticeships.
While this calls for all apprentices to be supervised by a fully qualified technician while performing tasks, that supervising technician does not need to watch every little move. However, they do need to be available for questions and ensure they have the instructions and resources to perform the job “safely, correctly, and efficiently.”
To prevent these apprentices from becoming part of the 20% who leave within two years, supervisors should find appropriate mentors who have the patience to teach others and step away from their own work.
“It’s not your best technician in the shop,” said Paul Cigala, an ExxonMobil commercial vehicle lubricants applications engineer. “Usually, it’s the technician who has been there for a while, knows the ins and outs, and can work closely with that new technician to help them.”
Cigala hosted a technician-related podcast with Arrants called “The Long Haul with Paula and George,” where he picked up several kernels of truth from fleet experts.
“Really focus on making sure that the technicians coming out of schools are prepared to get into the industry and are onboarded correctly,” Cigala instructed. “If he doesn’t feel like part of the family—maybe he’s struggling and nobody’s helping him or watching over his shoulder—he’ll be gone in less than a year and on to something else.”
TMC also has recommended practices to aid with technician training (RP 516A), setting up a performance review (RP 519), and shop review practices (RP 526).
In Part 3, we'll cover some ways the industry tackles training to further technicians' education.
About the Author
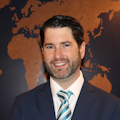
John Hitch
Editor-in-chief, Fleet Maintenance
John Hitch is the award-winning editor-in-chief of Fleet Maintenance, where his mission is to provide maintenance leaders and technicians with the the latest information on tools, strategies, and best practices to keep their fleets' commercial vehicles moving.
He is based out of Cleveland, Ohio, and has worked in the B2B journalism space for more than a decade. Hitch was previously senior editor for FleetOwner and before that was technology editor for IndustryWeek and and managing editor of New Equipment Digest.
Hitch graduated from Kent State University and was editor of the student magazine The Burr in 2009.
The former sonar technician served honorably aboard the fast-attack submarine USS Oklahoma City (SSN-723), where he participated in counter-drug ops, an under-ice expedition, and other missions he's not allowed to talk about for several more decades.