"AI toolbox" helps upskill technicians in the field
For more on technician training and AI:
When hiring a technician, shops and fleets know they can’t just grab anyone off of the street. Technicians are highly skilled, and it takes a not insignificant amount of time and money to send someone to a trade school, help them work through an apprenticeship or mentorship program, or even to provide continuous education to current technicians to keep their knowledge up-to-date.
This is where Airwave, a new AI-powered tool, comes in. Billed as an AI toolbox for technicians, Airwave is designed to allow technicians to easily find vetted resources to answer their questions while on the job, while also letting them add their own expertise in response to their peers, filtered through an AI interface that performs like a messaging app.
“Airwave is almost like a private AI that leverages the technology of a [large language modeling system] (LLM) and something that's called a RAG to make it really simple for [technicians] to find exactly what they need,” explained Pankaj Prasad, founder and CEO of Airwave.
When a company purchases Airwave, it allows them to input their personal documentation, from service orders and training videos to manuals, schematics, and part lists. Technicians can even record videos of their work from the field and add that as well.
Then, whenever a technician has a question, they can go to Airwave and receive answers from their peers and the shop’s documentation. This streamlines the processes they might have followed anyway when confronted with a problem, but with better sourcing than simply turning to YouTube or online forums. And at the same time, this allows Airwave to help upskill current technicians and train up new ones.
Using Airwave to upskill
With the current generation of technicians beginning to look toward retirement, many shops and fleets may be about to lose their master technicians without a quick way to replace them and their knowledge. But Airwave offers another way to help upskill current technicians with access to older techs’ expertise.
“What does it mean to be an expert technician?” Prasad asked. “It really is just recall. And if you can codify that into a product and make it super simple, you give every technician the opportunity to become an expert, without having to spend years at different skill levels collating that.”
Airwave does this by offering technicians step-by-step instructions pulled from a shop’s manuals, parts lists, and other technicians’ responses to questions (and in over 50 languages, too). And even more so, the AI can show technicians where it got its information, whether its from an earlier response to the same question from a senior technician or the specific page of a manual. In this way, the app gives technicians more resources to learn quickly but doesn’t rob them of the chance to improve by giving them an answer with no context.
After all, Prasad said he always tells users that “AI isn't going to solve the problem for you, but if you can frame the problem and ask a question for some information to help you solve that problem, it's unbelievable at retrieving all relevant information,” he said. “But it's still upon the technician to take that information and apply it to what they see, hear, and feel, because AIs don't do that today.”
As an example, perhaps a shop has a branch in two different geographical regions. If a technician asks a question and two others have responded to that question in Orlando, Florida, and Chicago, Illinois, then the AI, called Jarvis, will provide the original poster with both responses.
“Jarvis doesn't decide which is the better answer,” Prasad emphasized. “It just surfaces both, and then it's up to the technician to determine which one is more relevant.”
Airwave and onboarding
Ok, but what if the technician asking a question doesn’t have a few years of work under the belt. Is Airwave still helpful to them?
“When we think about a technician straight out of school versus someone that's gone through an apprenticeship, there's so much for them to learn,” Prasad explained. “For them to get to a master level, they have to go through and experience all of the different types of fixes. In some industries that can take years.”
But Jarvis can help those techs simply by giving them access to a repository of tribal knowledge that they would have had to painstakingly learn themselves.
And even more so, Airwave can offer new techs a non-judgmental space to ask questions when they’re just starting out. As an example, Prasad said that one Airwave client did a lot of onboarding, typically almost a dozen technicians every month or two. For the new hires, the client said the candidates who asked the most basic questions tended to do the best. But not everyone asks those questions out of fear of looking unqualified, which could leave them starting their job on the wrong foot.
“What [those clients saw] is that new technicians will ask hundreds of questions in the first couple of weeks because they're building context for not only the products that they're now having to service, but also how the company does it,” Prasad said. This results in “faster onboarding” and “faster skill development,” he added.
And as an added benefit of codifying new techs’ FAQs, this also frees up the master technicians who would’ve been answering those questions. Prasad described a case like this where a company was worried that one of their workers, Don, was going to retire soon, taking all of this 40 years of experience with him. After discarding the idea of hiring a film crew to follow him around for a couple weeks, they landed on using Airwave instead.
“Over the course of a couple of months, all of the repeat questions that Don was answering on a regular basis were now cataloged, and Don was now just doing the extreme exceptions,” Prasad concluded.
About the Author
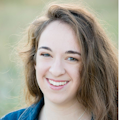
Alex Keenan
Alex Keenan is an Associate Editor for Fleet Maintenance magazine. She has written on a variety of topics for the past several years and recently joined the transportation industry, reviewing content covering technician challenges and breaking industry news. She holds a bachelor's degree in English from Colorado State University in Fort Collins, Colorado.