There are two different types of natural gas engines and systems for the heavy duty natural gas market, says Paul Pate, training manager at the Natural Gas Vehicle Institute (NGVi), a provider of training and consulting on natural gas as a transportation fuel (www.ngvi.com). They are: spark ignited – the most widely used – and compression ignited.
Compression-ignited systems, which only exist as dual-fuel systems, come in two types: substitution systems and high-pressure direct injection (HPDI) systems, a proprietary technology developed by Westport (www.westport.com), he notes.
SUBSTITUTION SYSTEMS
Substitution systems simply add natural gas to the diesel fuel, “substituting” a percentage of the diesel with natural gas, explains Pate. They run either on natural gas mixed with diesel or pure diesel, but will not run on natural gas only.
The substitution percentage of diesel with natural gas ranges between 0 and 65 percent, depending upon load and operating conditions.
Substitution systems account for the majority of dual-fuel diesel/natural gas engines, he says.
HPDI
High-pressure direct injection systems are vastly different, says Pate. They use natural gas as the primary fuel, along with a small amount of diesel as a pilot ignition source, or "liquid spark plug."
Like a dual-fuel engine, an HPDI system relies on diesel for combustion to occur.
HPDI technology involves the injection of both diesel and natural gas to be delivered at high pressure directly into the combustion chamber at the end of the compression stroke.
Westport says HPDI technology maintains the fundamental efficiency and performance of industry-prevalent diesel engines, but with a diesel substitution of more than 90 percent.
HPDI systems, Pate says, are intended for high torque and high horsepower applications.
About the Author
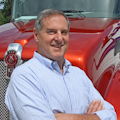