Much has changed since the diesel engine was developed by German engineer Rudolf Diesel in 1896 – in an attempt to improve upon the inefficient steam engines common in his day, especially over the past decade or so. Today’s heavy duty diesel engines have evolved to provide greater efficiency and produce less carbon (greenhouse gas) emissions.
This has been brought about by engine design changes which “gradually transitioned the image of diesel – rooted in vehicle technologies dating back to the 1970s – as a “slow, smoky, dirty, noisy, heavy and smelly engine” to a responsive, more efficient and much cleaner engine, observes DieselNet (https://dieselnet.com), an online information service exclusively devoted to diesel engines and emissions.
Changes
Changes made included:
- Optimizing the combustion chamber design.
- Increasing the injection pressure in the fuel injection system to help with engine performance, emissions and noise.
- The use of charge air systems to supply additional combustion air during engine acceleration.
- Advanced fuel injection (common rail systems and electronic unit injectors) to manage fuel injection electronically for more precise control of the combustion process.
- Turbocharging, which uses what would have been wasted energy in exhaust gases to power turbines that pressurize air in the engine’s cylinder, allowing the engine to produce more power.
“Diesels initially enjoyed modest emission regulations,” according to DieselNet.
That changed in the 1990s when diesel emission standards – enacted to reduce emissions of nitrogen oxides (NOx) and particulate matter (PM) – became increasingly difficult to meet.
Strict Emissions Regulations
In December 2000, the U.S. EPA adopted a rulemaking entity to establish stringent federal emissions standards for model year 2007 and later heavy duty highway engines. The U.S. EPA Emissions Standards for Heavy Duty Diesel Engines was intended to reduce emissions from on-road heavy duty trucks and buses by up to 95 percent, plus cut the allowable levels of sulfur in diesel fuel by 97 percent.
These standards included new rigorous limits for PM and NOx. The PM emission standard took full effect in 2007. The NOx standard was phased-in between 2007 and 2010.
Owners and operators of trucks powered by the more complex EPA-compliant heavy duty diesel engines experienced a number of problems with these engines. Among these, a high rate of engine- and fuel-related problems, resulting in unplanned downtime. The problems were caused by the technology that was designed to reduce emissions from heavy duty truck engines.
In August 2011, U.S. EPA and the National Highway Traffic Safety Administration (NHTSA) issued their Phase 1 Greenhouse Gas Emissions Standards and Fuel Efficiency Standards for Medium and Heavy Duty Engines and Vehicles. The agencies said these standards were designed to “improve fuel efficiency and cut carbon pollution to reduce the impacts of climate change, while bolstering energy security and spurring manufacturing innovation.” The standards affected model years 2014 to 2018.
In August 2016, the two agencies issued the Greenhouse Gas Emissions and Fuel Efficiency Standards for Medium and Heavy Duty Engines and Vehicles - Phase 2. It “promotes a new generation of cleaner, more fuel efficient trucks by encouraging the development and deployment of new and advanced cost-effective technologies,” said EPA and NHTSA.
The vehicle and engine performance standards cover model years 2021 to 2027 for semi-trucks, large pickup trucks, vans and all types and sizes of buses and work trucks. The standards are being rolled out in three stages: 2021, 2024 and 2027.
The EPA and NHTSA standards also cover model years 2018 to 2027 for certain trailers. This is the first time trailer OEMs have been regulated by U.S. EPA.
Up to the Challenge
How is the industry meeting these objectives in such a compressed period of time? Through innovation.
Take PACCAR – one of the premier diesel engine manufacturers in the world and a global technology leader in the design, manufacture and customer support of light, medium and heavy duty trucks under the Kenworth, Peterbilt and DAF nameplates, for example.
Meeting the vehicle and engine performance standards “involves the use of materials and components that provide the right combination of strength and weight; advanced engine control technology; and a commitment to making the refinements necessary to exceed customer expectations,” says Landon Sproull, vice president, powertrain, PACCAR (www.paccarpowertrain.com).
Diesel Engine Evolution
“SCR (Selective Catalyst Reduction) in conjunction with a DPF (diesel particulate filter) has become the established aftertreatment technology for meeting U.S. EPA and NTHSA emissions standards,” says PACCAR’s Sproull. “More than 500,000 vehicles in the industry are successfully performing with SCR and DPF technology today.
“Regulated emissions have been reduced to near-zero levels with no visible smoke emitted from the engine. A white handkerchief will stay white when held over the exhaust pipe.”
Advanced electronic control technology provides more precise combustion timing, reduced emissions and better fuel economy, he points out. A smart engine and emission control system can communicate real-time performance and diagnostic information to the customer and dealer efficiently and in simple language.
“One of the most important developments in the North American engine market is the ability to produce more power and performance from a smaller displacement engine,” notes Sproull. “Engines with smaller displacements can provide power and torque that are comparable to larger engines, with the added benefits of less weight, better fuel economy and reduced emissions.”
Sproull adds that engine life is increasing. A B50 engine – once an industry standard for average life to overhaul – meant that at 1 million miles, 50 percent of the engines would need a rebuild. In 2010, PACCAR’s MX engine platform was designed with a B10 life, meaning that 90 percent of these engines will go beyond 1 million miles without the need for a major overhaul.
The advantages of proprietary engines have enabled truck OEMs, like Peterbilt and Kenworth, to better integrate the engine to the vehicle. An example of this collaborative approach is easier access to preventive maintenance items on the truck, like oil and fuel filters.
“Industry-leading serviceability of PACCAR engines and trucks is achieved through intense design collaboration of PACCAR engineers and dealer and customer technicians,” Sproull says.
Through technological innovation achieved by collaboration between the U.S. DOE, national labs, universities, and the private sector, engine manufacturers have been able to implement a variety of state-of-the art technologies that ensure diesel engines are running cleanly and efficiently, he says.
More to Come
To be sure, heavy duty diesel engine research and development to increase understanding of the combustion process and emissions will continue, and this will inevitably lead to more technological innovation.
In turn, this will help develop even cleaner and more efficient engines and promote national goals, such as protecting public health and promoting energy security.
About the Author
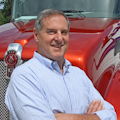