Filters are a basic part of keeping engines healthy and efficient and vehicles on the road. But just like vehicles, some are more suited for heavy-duty operation while others are better for light-duty. To discuss the differences between the two and get some tips on heavy-duty filter maintenance and the future for filters, we sat down with Anan Bishara, CEO of Premium Guard Inc, an automotive manufacturer and supplier.
Fleet Maintenance: What’s different about filters for the heavy-duty industry versus the light-duty one?
Anan Bishara: Filters for heavy-duty (HD) applications differ significantly from those in light-duty (LD) vehicles due to two key factors: design of commercial engines and operating environments. These differences affect the specification of the various filters:
- Engine Structure and Performance: HD engines are built for prolonged high-load use under extreme conditions. They have larger displacements, higher oil capacities, and run at higher compression, requiring more robust filtration, while LD engines prioritize fuel efficiency, lower emissions, and operate under lighter, intermittent loads—requiring smaller, less rugged filters.
- Operating Conditions & Service Life: HD engines run for extended periods under load, requiring filters that perform under heat, vibration, and stress. They also require longer filter life, they reduce downtime and support a lower Total Cost of Ownership (TCO), often monitored via onboard diagnostics.
- HD oil filters handle higher flow rates and extended drain intervals. They require high dirt-holding capacity and reinforced construction of advanced media for long-term efficiency.
Otherwise, air filters are designed for dusty, off-road, and industrial conditions. Often coming in two stages (primary + secondary), they offer higher dust-holding capacity as well as resistance to pulsation and airflow surges. Additionally, fuel and diesel filters are built with synthetic fiber micron ratings media to protect the injection systems. Most importantly, the filters must include water separation capabilities.
FM: What kind of damage or faults can result if filters aren’t changed when they should be?
AB: Neglecting timely filter replacement can lead to significant and costly damage in heavy-duty vehicles. Clogged air filters, for instance, can reduce engine performance, increase fuel consumption, and cause excessive soot buildup in the combustion chamber. Similarly, dirty fuel filters can allow particulates and water into the fuel system, damaging fuel injectors and pumps—components that are expensive and labor-intensive to replace. Hydraulic and oil filters that are not changed as scheduled can lead to abrasive wear of internal components, reduced lubrication effectiveness, and, eventually, catastrophic failure of critical systems like transmissions and engines.
FM: Are there any surprising downstream symptoms that can result from improper filter maintenance?
AB: Yes, improper filter maintenance—whether due to delayed replacement or the use of low-quality filters—can lead to a range of unexpected issues that are not immediately attributed to filtration.
For example, a clogged or overdue air filter can disrupt airflow readings and trigger sensor errors in modern engine management systems, potentially resulting in warning lights or even limp mode activation. A fuel filter that is either saturated or of insufficient quality may fail to separate water effectively, leading to injector misfires, hard starting, or performance issues that resemble electrical faults.
In the case of oil filters, failure to replace the filter on time can result in the filter reaching capacity and entering bypass mode, allowing unfiltered oil to circulate through the engine. This can accelerate engine wear and lead to long-term damage, even though the issue may not be immediately noticeable.
In hydraulic systems, bypassed or clogged filters—often due to neglected service intervals or inferior construction—can cause erratic equipment behavior, reduced responsiveness, or overheating. These symptoms may be misdiagnosed as mechanical or electronic faults when they are, in fact, filtration related.
Proper filter maintenance—including timely replacement and the use of high-quality filters that meet or exceed OE requirements—is essential to ensure system reliability and preventing costly downstream failures.
FM: How can shops make sure they’re changing filters when they should?
AB: Shops can stay ahead of filter maintenance by implementing strict adherence to OEM-recommended service intervals, maintaining detailed vehicle maintenance logs, and utilizing fleet management software that tracks service life for each filter type. Additionally, training technicians to recognize signs of filter degradation—such as pressure drop indicators, visual inspection cues, or performance symptoms—is essential. Some modern filtration systems also offer sensor-based monitoring that alerts maintenance personnel when filter restriction reaches critical levels, taking the guesswork out of the process.
FM: What’s the process to change out an HD filter? Are there any pitfalls technicians should know about?
AB: Changing a filter in heavy-duty equipment generally involves more steps and caution than in light-duty vehicles due to the system complexities and higher fluid volumes. The basic process includes system depressurization, filter removal (avoiding contamination of the system), inspection of the old filter for unusual debris, installation of a properly lubricated new filter, and system priming or bleeding if necessary. A common pitfall is failing to verify that old gasket material was completely removed, which can lead to sealing failures. Over- or under-tightening filters can also cause leaks or damage. For fuel and hydraulic filters, failing to properly prime the system after replacement can result in air lock or pump cavitation.
FM: What kind of trends do you anticipate for the future of filtration technology?
AB: The future of filtration technology is being shaped by a combination of environmental regulations, advances in materials science, lowering the TCO, and the evolving demands of modern engines and equipment. Key trends include:
- Advanced Filter Media: Next-generation filter media—such as nanofiber composites and multilayer synthetics—will become more prevalent. These materials offer higher efficiency with lower pressure drop, improved dust-holding capacity, and enhanced water separation in fuel systems. These advancements will support longer service intervals and better protection, especially for high-performance and heavy-duty applications.
- Longer Service Life and Sustainability: As fleets push to reduce downtime and total cost of ownership (TCO), filtration systems will be engineered for extended drain intervals and longer lifecycle performance. Hydrogen systems will introduce entirely new filtration challenges for purity and moisture control.
Filtration technology is becoming smarter, cleaner, and more efficient. The industry will continue moving toward longer-lasting, sensor-enabled, and environmentally responsible solutions—with filtration playing a critical, though often invisible, role in protecting engines, machines, and people.
About the Author
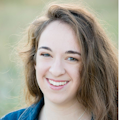
Alex Keenan
Alex Keenan is an Associate Editor for Fleet Maintenance magazine. She has written on a variety of topics for the past several years and recently joined the transportation industry, reviewing content covering technician challenges and breaking industry news. She holds a bachelor's degree in English from Colorado State University in Fort Collins, Colorado.