How VMRS unlocks the power of maintenance categorization
Maintaining a fleet isn’t just about fixing what’s broken; it’s also about predictive strategies, cost control, and optimizing every facet of the maintenance process. One key tool in achieving all this is maintenance categorization—especially within the framework of Vehicle Maintenance Reporting Standards (VMRS). When used correctly, fleets can leverage maintenance categorization for enhanced expense tracking, comprehensive fleet health overviews, and real-time total cost analysis. And as technology advances, pairing this data with fleet management systems will drive even more efficiencies through predictive maintenance.
What is VMRS?
VMRS is basically a universal language for commercial vehicle repair, connecting fleet managers, technicians, OEMs, and those responsible for equipment maintenance. This is done through numerical codes representing the system, assembly, and/or component affected. For instance, code key 31 designates the vehicle system (e.g., air conditioning), code key 32 refers to the assembly (e.g., front brakes), and code key 33 specifies the component (e.g., diesel particulate filter). This method enables clear communication and serves as a tool for maintenance categorization.
Read more: TMC: VMRS Adapts to Standardize Predictive and Prognostic Maintenance Alerts
This 'language' was developed for heavy-duty vehicles in 1970 by the American Trucking Associations’ Technology and Maintenance Council (TMC). Since then, the precision maintenance coding and reporting tool has offered a scalable and manageable service analytics solution for fleets. TMC periodically updates the coding as equipment and technology advance.
The true power of VMRS, however, lies not just in identifying vehicle components but also in categorizing the reasons for repair and work accomplished. Code key 14 denotes the reason for repair, with subcategories like maintenance, management decision, and outside influence, while code key 15 specifies work accomplished, allowing technicians to quickly check off the work performed.
Implementing maintenance categorization in fleet management also offers a standardized method for documenting service work. This standardization allows for the creation of clean service records and detailed histories, aiding managers in adjusting preventive maintenance (PM) schedules to extend asset lifespans and improve asset ROI.
Cost analysis and clean reporting
Because maintenance categorization provides a detailed breakdown of maintenance costs, fleets can quickly discover where time and money are being spent the most. It also helps fleets identify areas of excessive repair spend, making corrective actions possible and increasing overall uptime. Moreover, it ensures that everyone involved, from drivers to accountants, “speaks the same language,” reducing the chance of data, reporting, and billing errors around fleet maintenance.
By analyzing service costs over time, fleets can identify patterns, such as recurring issues or components that frequently require attention. This knowledge is invaluable for budgeting and cost forecasting as well as strengthening PM schedules, allowing managers to allocate resources more effectively. The comprehensive data provided by maintenance categorization goes beyond the immediate cost of repairs; though it includes factors like downtime, impact on other components, and overall asset performance, allowing managers to make informed decisions about asset replacement and strategic planning for long-term cost savings.
One user of Fleetio's maintenance management platform found using a VMRS code key inceased total maintenance scheduled by 17%. Maintenace service cost also decreased by 13%. This equated to $85,000 in savings.
Predictive maintenance
The consistency and accuracy of maintenance categorization data enhance its role in actionable reporting, making it a powerful tool for informed decision-making. For example, pairing maintenance categorization with robust fleet management software (FMS) adds a layer of predictive analytics, giving fleets and shops foresight into pending equipment issues. VMRS-compatible software collects and categorizes such data as the aforementioned parts/systems affected, reasons for repair, repair sites, work accomplished, and technician failure. Fleet managers can also leverage this data to identify repetitive issues, optimize routes based on maintenance needs, and address specific areas of concern.
Read more: How predictive maintenance can save fleets a fortune
Utilizing maintenance categorization in FMS also ensures consistency across in-house and third-party service, allowing fleets to build detailed asset service histories regardless of whether they outsource maintenance, perform services in house, or even a mixture of the two. This standardization is crucial for identifying problem areas like cost inflation, extended downtime, recurring mechanical issues, and inefficient PM.
Fleet health and lifecycle
Maintenance categorization can also give fleet managers a better understanding of total fleet health, as well as the health of individual assets. Being able to identify which systems or components are prone to issues allows for proactive maintenance and, furthermore, allows fleets to see common issues across specific makes and models, which could in turn alter future procurement plans. Maintenance categorization data can also help fleets pinpoint when it’s more cost-effective to replace a component than to continue repairing it, and when it’s more costly to maintain an asset than to replace it.
The road ahead
VMRS-based maintenance categorization is not just a coding system; it’s a major tool in successful fleet management, offering a universal language for maintenance-related communication and standardizing data for consistency so fleets can create predictive strategies.
As the fleet industry moves towards increased digitization and predictive analytics, embracing maintenance categorization becomes not just a choice but a necessity for those seeking to unlock savings in their fleet operations. By understanding asset costs, monitoring fleet health, and conducting total cost analysis, fleet managers can steer their operations towards optimal efficiency and sustained cost control.
Rachael Plant is a content marketing specialist for Fleetio, a fleet management software company that helps organizations track, analyze, and improve their fleet operations.
About the Author
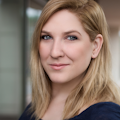
Rachael Plant
Rachael Plant is a content marketing specialist for Fleetio, a fleet management software company that helps organizations track, analyze and improve their fleet operations.